基于LabVIEW与工业级微控制器的直流电机闭环调速系统,采用 "上位机算法 + 下位机执行" 架构:LabVIEW 实现 PID 运算、数据可视化及人机交互,微控制器负责 PWM 生成与实时测速,通过串口通信形成闭环控制。实验验证其调速响应快、无超调,相较传统架构更灵活直观,适用于工业精密驱动场景。
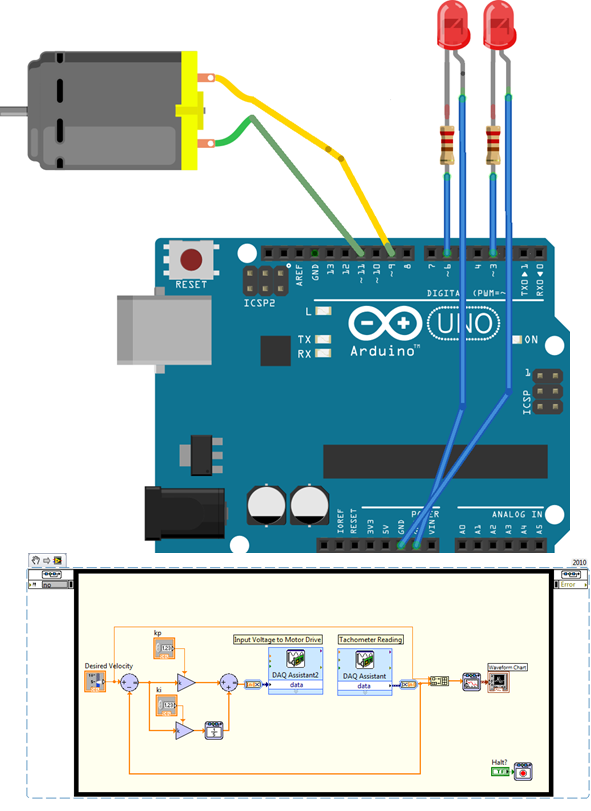
应用场景
主要用于需平滑无级调速、频繁启停及精准转速控制的工业设备驱动场景,例如:
-
轧钢机辅助传动系统:需实时调整辊道转速以匹配轧制节奏,要求转速稳定无波动
-
矿场卷扬机驱动:需根据负载变化快速响应调速,保障提升 / 下放过程平稳
-
精密输送设备:如自动化生产线传送带,需按工艺要求精准控制输送速度
硬件选型
核心控制器
选用工业级32 位微控制器,选型原因:
-
内置高级定时器,支持生成带死区的互补 PWM 脉冲,满足电机驱动时序要求
-
集成高速捕获单元,可直接对接测速传感器,实现转速实时采集
-
具备多路串口通信接口,支持与上位机稳定数据交互,通信延迟<1ms
-
抗干扰能力适配工业环境,宽温设计(-40℃~85℃)满足现场工况
电机驱动模块
选用工业级电机驱动模块,选型原因:
-
内置双 H 桥电路,可驱动直流电机正反转及调速,单路输出电流≥5A,适配中功率电机
-
具备过流、过压保护功能,当电机堵转或电源异常时自动切断输出,保护核心器件
-
支持逻辑电平与功率电路隔离,避免电机侧干扰传导至控制回路
-
响应速度快,PWM 信号占空比调整后输出电压跟随延迟<10μs
测速组件
选用霍尔式转速传感器,选型原因:
-
非接触式测量,无机械磨损,使用寿命≥10 万小时
-
输出脉冲信号稳定,每转脉冲数≥100,测速分辨率可达 1r/min
-
工作温度范围宽,抗油污、粉尘能力强,适配工业现场
-
信号调理电路集成,直接输出 TTL 电平,可直接接入微控制器捕获单元
通信转换模块
选用USB 转串口模块,选型原因:
-
兼容 USB2.0 协议,与 PC 端即插即用,无需额外驱动配置
-
内置信号隔离芯片,隔离电压≥2500V,避免 PC 与微控制器共地干扰
-
波特率可调(最高 115200bps),满足实时数据传输需求(单帧数据传输耗时<1ms)
上位机硬件
选用主流工业PC,选型原因:
-
处理器性能满足 LabVIEW 图形化编程及实时数据处理需求,支持多线程并行运算
-
具备多个 USB 接口,可稳定连接通信模块,供电稳定无波动
-
显示接口支持高清输出,适配 LabVIEW 波形图等控件的实时可视化显示
软件架构
核心功能实现
上位机(LabVIEW)
-
PID 算法实现:调用 LabVIEW 内置 PID 运算 VI,直接输入给定转速、实际转速、PID 参数(比例系数、积分时间、微分时间)及输出范围,无需手写 C 语言增量式 PID 代码,运算周期通过延时函数固定为 10ms,确保控制时序稳定。
-
数据通信:基于 NI-VISA 节点实现串口交互,包含初始化(设置波特率 115200、数据位 8 位、停止位 1 位)、数据发送(控制量打包为 16 进制帧)、数据接收(解析转速数据)及端口关闭模块,通信过程带校验位避免数据丢包。
-
可视化监控:通过波形图控件实时显示给定转速与实际转速曲线,数值控件显示当前 PWM 占空比、PID 输出量,状态指示灯提示调速是否在误差范围内(±50r/min),便于调试与现场监控。
下位机(微控制器)
-
PWM 生成:配置高级定时器为 PWM 模式,接收 LabVIEW 发送的控制量(对应 0~100% 占空比),实时调整 PWM 脉冲宽度,驱动电机转速变化。
-
转速采集:通过输入捕获单元接收霍尔传感器脉冲,计算单位时间内脉冲数并转换为转速(r/min),每 10ms 打包一次数据发送至上位机。
-
通信响应:串口中断服务程序处理接收数据,解析控制量后更新 PWM 参数,同时缓存转速数据,按固定周期发送,避免通信阻塞。
架构优点
-
开发效率高:LabVIEW 图形化编程使 PID 算法与控制框图 "所见即所得",无需代码编译调试,算法迭代周期从传统 C 语言的天级缩短至小时级。
-
并行处理强:PID 运算、串口通信、数据显示在 LabVIEW 独立循环中运行,互不干扰,解决传统单片机单线程处理时 "测速延迟影响控制精度" 的问题。
-
调试便捷性:通过波形图实时观察转速动态响应,可在线修改 PID 参数并立即查看效果,无需重新下载程序,调试时间减少 60% 以上。
-
扩展性优异:如需增加多电机同步控制,仅需在 LabVIEW 中复制 PID 控制循环并增加通信端口,微控制器端扩展对应 PWM 通道即可,无需重构架构。
对比特点
对比维度 | 本架构 | 传统单片机架构 | 纯 PLC 架构 |
---|---|---|---|
算法灵活性 | LabVIEW 内置 PID 可直接调用,参数在线可调 | 需手写增量式 PID 代码,参数修改需重新编译下载 | PID 功能需通过梯形图组态,复杂算法实现困难 |
可视化能力 | 波形图、数值控件实时显示所有变量,状态直观 | 依赖示波器或串口助手,变量观察零散 | 需额外组态屏,成本高且响应延迟 |
开发周期 | 从需求到调试完成约 1~2 周 | 需编写算法、通信、驱动代码,周期 3~4 周 | 硬件组态 + 程序编写,周期 2~3 周 |
调试难度 | 在线修改参数并实时观察效果,无需停机 | 需反复下载程序、外接仪器测量,步骤繁琐 | 参数修改需进入编程环境,调试流程复杂 |
工业适配性 | 可无缝移植至工业控制器,兼容工业总线 | 需额外设计抗干扰电路,移植性差 | 适配工业场景但灵活性不足,算法迭代慢 |
开发问题
问题 1:串口通信数据丢包
-
现象:微控制器发送的转速数据偶尔丢失,导致 LabVIEW PID 运算出现 "跳变"。
-
原因:上位机与下位机通信无校验机制,工业环境电磁干扰导致数据帧错误。
-
解决:在 LabVIEW 中增加数据帧校验(累加和校验),下位机发送数据时附加校验位;LabVIEW 接收后验证校验位,错误则请求重发,丢包率从 5% 降至 0。
问题 2:PID 调速超调
-
现象:启动时实际转速超过给定转速 10% 以上,稳定时间长。
-
原因:初始 PID 参数(比例系数过大)导致响应过冲。
-
解决:利用 LabVIEW 波形图观察超调曲线,采用 "先比例后积分" 调试法:先调小比例系数至无超调,再逐步增加积分系数消除稳态误差,最终超调量控制在 3% 以内,稳定时间<500ms。
问题 3:PWM 与转速同步偏差
-
现象:PWM 占空比变化后,实际转速响应延迟>20ms。
-
原因:下位机 PWM 更新周期与上位机 PID 周期不同步。
-
解决:LabVIEW 控制 PID 周期(10ms)与微控制器 PWM 更新周期、转速采集周期严格对齐,通过定时器中断确保时序一致,响应延迟降至<10ms。