关键词:构型、能量流、DM-i
一、发展历史:从DM1到DM5的技术跃迁
比亚迪DM(Dual Mode)技术始于2008年,其发展历程可划分为五代,核心目标始终围绕"油电协同"与"高效节能"展开:
- DM1(2008):首搭F3DM车型,采用1.0L三缸机+双电机串并联架构,实现纯电、增程、混动三模式,但因成本高、技术不成熟未获市场认可。
- DM2/DM3(2013-2018):以性能为导向,引入P3+P4双电机布局及BSG电机,代表车型为秦DM、唐DM,但馈电油耗高、NVH差的问题突出。
- DM-i(2021):技术路线回归节能,采用大电机+大电池+高效阿特金森发动机,取消传统变速箱,核心为"以电为主",亏电油耗低至3.8L/100km,成为市场爆款。
- DM5(2024) :第五代技术实现46.06%全球最高热效率、2.9L亏电油耗及2100km综合续航,通过全温域热管理、智电融合架构实现系统级突破。
二、构型原理:双电机串并联与极致集成
DM-i的核心架构为P1+P3双电机串并联系统,由以下模块组成:
- 插混专用发动机:1.5L阿特金森循环(热效率43%-46.06%),取消轮系附件,专注高效发电区间。
- EHS电混系统:集成发电机(P1)、驱动电机(P3)、单级减速器及电控,功率密度达75kW/L,综合工况效率92%。
- 功率型刀片电池:磷酸铁锂体系,支持16C放电/5C回馈,能量密度提升15.9%,集成于专用混动平台底盘。
- 无传统变速箱:通过离合器实现发动机直驱,仅保留单档位,简化传动路径。
DM-i技术示意图
比亚迪DM-i(Dual Mode Intelligent)混动技术是其插电式混合动力系统的核心,其"以电为主、油为辅"的设计理念,实现了高效能与低油耗的平衡。
DM-i系统主要由以下四部分构成:
◽ ** 电机组件结构:**双电机(主电机驱动+辅电机发电)协同,在第五代DM-i技术中引入了行星齿轮减速结构,可以实现双电机同时驱动。
◽ **机电耦合结构:**包含离合器、差速器、以及多个单极减速器,用于实现动力传输与切换。
◽ **内燃机端:**比亚迪自研发动机:1.5L混动发动机-以极致热效率支撑DM-i系统的低油耗优势;1.5T骁云发动机-通过涡轮增压与智能控制实现动力与能效的平衡;2.0T发动机-则聚焦高性能市场,兼顾动力输出与燃油经济性。
◽ **动力输出端:**将DM-i系统的动力输出到驱动轮,实现车辆行驶。
三、能量流模式:四工况动态优化-5种工作模式
DM-i系统根据车速、负载及SOC动态切换模式,实现全局效率最优:
- EV纯电模式:电池直接驱动电机,发动机停机,适用于低速低负载场景。
- HEV串联(增程)模式:发动机带动P1电机发电,电能驱动P3电机或存储于电池,适用于中低速及馈电状态。
- HEV并联模式:发动机直驱+P3电机辅助,用于高速超车等高功率需求场景。
- 发动机直驱模式:车速>70km/h时,离合器结合,发动机直接驱动车轮,避免能量二次转换损失。
DM-i插混技术一共有5种工作模式
** 纯电模式**
** 内燃机直驱模式**
**串联模式 **
**动能回收模式 **
**并联模式 **
模式一------纯电模式
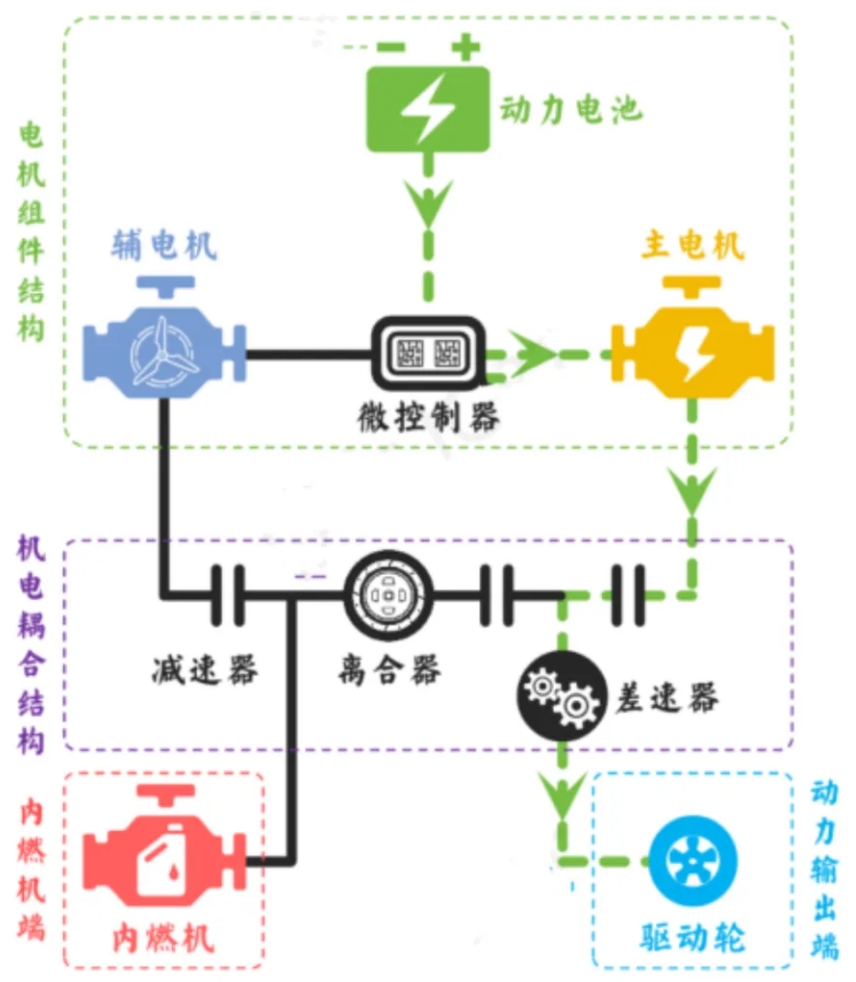
能量流:动力电池直接为主电机(驱动电机)供电,内燃机和辅电机(发电机)完全关闭,车辆由主电机单独驱动,驾驶噪音极小,具体可分为以下三种纯电模式:
◽ 纯电经济模式(EV-ECO):控制器缓慢增大电机电流优化电能消耗,延长续航里程。
◽ 纯电舒适模式(EV-NORMAL):电机以适中功率输出兼顾电能消耗和动力加速。
◽ 纯电运动模式(EV-SPORT):电机以最大功率输出提供瞬时加速性能,适合急加速需求。
适用场景:低速城市通勤(如拥堵路段)、短途行驶(电池电量充足时)。
刀片电池的高放电效率(94%)和低内耗特性,保障了纯电续航的稳定性,尤其适合城市工况下85%的纯电驱动占比。
内燃机直驱模式
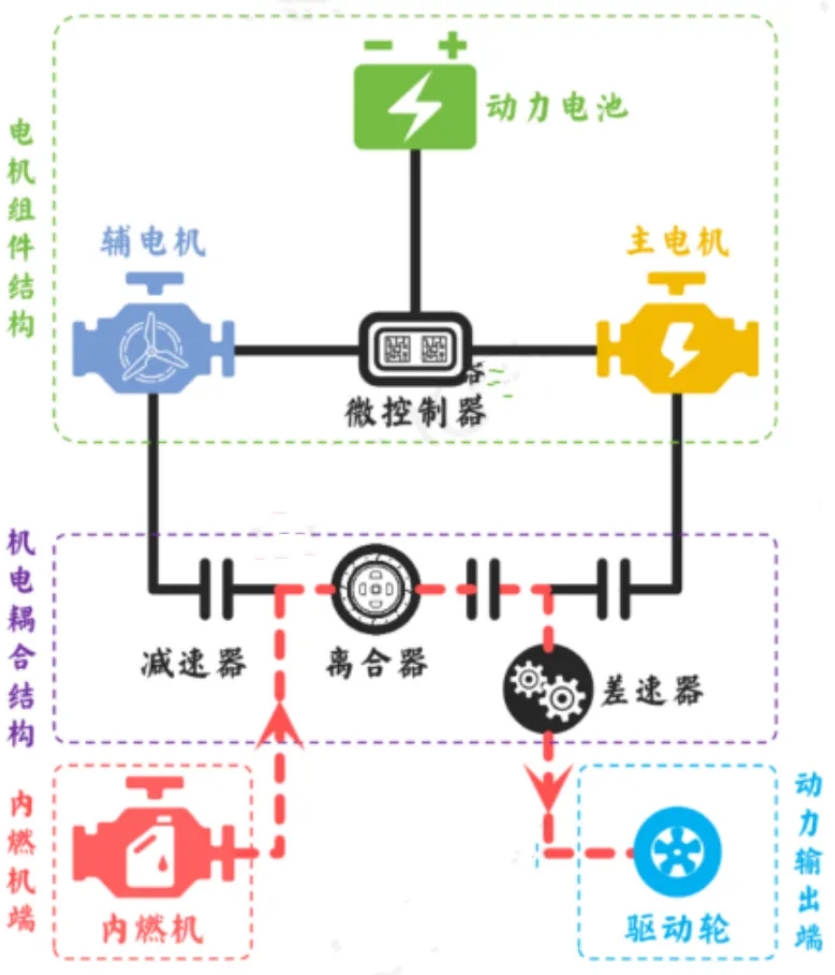
◽ 能量流:内燃机输出轴通过离合器、减速器(或行星齿轮组)与驱动轮机械连接,形成"内燃机→离合器→减速器/行星架→驱动轮"的直接驱动链路。
该模式适用场景如下:
◽ 高速巡航:内燃机直接驱动车轮,避免电能多次转换的损耗,油耗显著降低。第五代DM技术进一步优化了内燃机高效区间,直驱模式下综合续航可达2100公里。
◽ 中高负荷需求:如长距离爬坡或超车时,直驱模式可避免电机高负荷放电导致的电池衰减,同时通过内燃机与主电机(驱动电机)并联输出动力。
◽ 低电量:当电池电量低于SOC保护值时,系统优先切换至直驱模式,减少充放电损耗,同时通过辅电机(发电机)调节内燃机负荷,维持高效运行。
内燃机直驱模式将能量转换环节从两次(机械→电→机械)减少为一次(机械→机械),传动效率提升至90%以上相比传统增程式混动能耗降低约12%。
串联模式
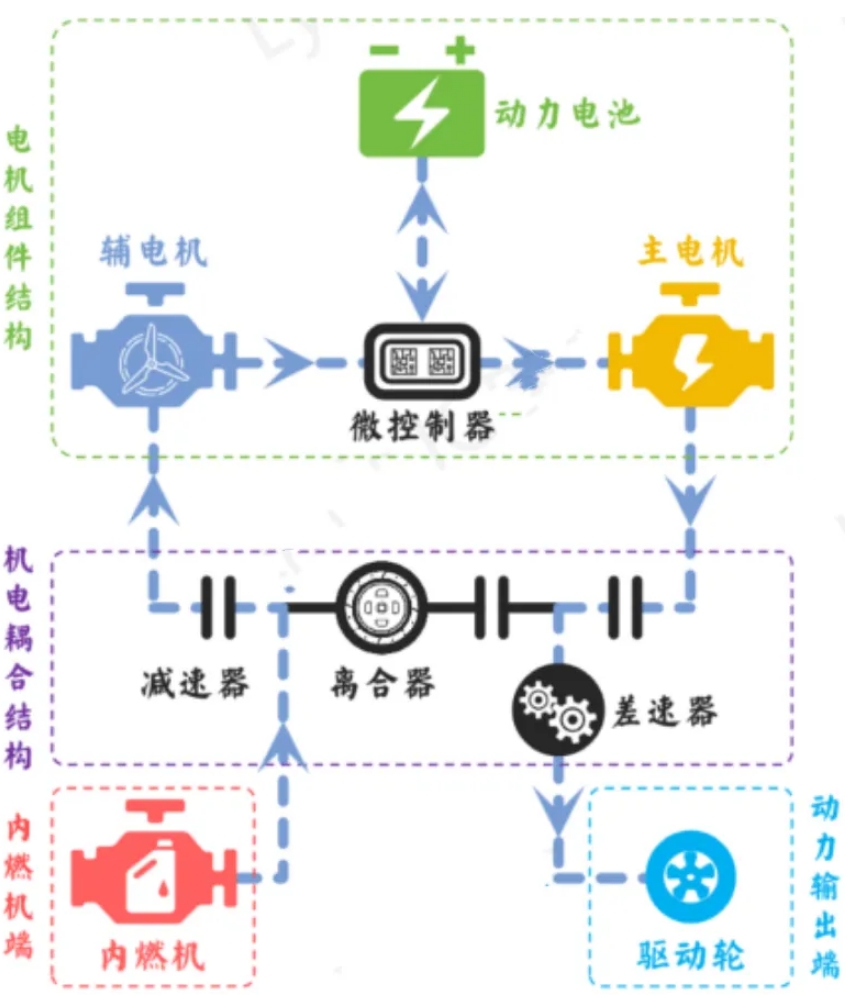
◽ 能量流:该模式区别于内燃机直驱模式,内燃机启动,但不直接驱动车轮,而是带动辅电机(发电机)发电,优先供电给主电机(驱动电机),剩余电能存入动力电池。
该模式适用场景如下:
电池电量不足(SOC低于保护设定值)且车速较低时(如持续拥堵或中低速巡航)。
该模式下,能量转换环节为两次(机械→电→机械),比较类似传统增程式混动,但此时内燃机始终运行在高效区间(2000-4000rpm,热效率43%-45%),可避免低效工况的燃油浪费。
动能回收模式
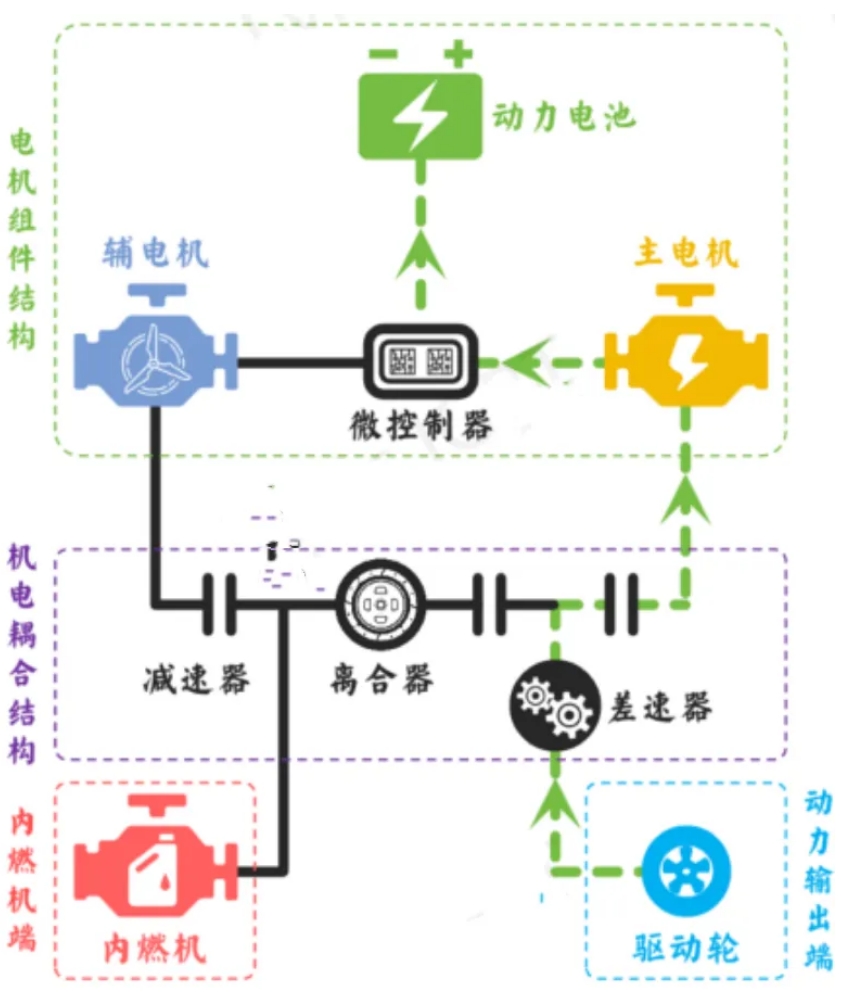
◽ 能量流:纯电模式能量流的反向路径,主电机(驱动电机)转换为发电机,将行驶过程中的动能转化为电能存储至动力电池。部分车型支持自适应回收强度调节,根据路况预判优化回收效率。
该模式适用场景如下:制动、滑行或下坡路段。
动能回收模式的激活依赖于多维度传感器数据与智能能量管理系统的协同决策,该模式触发条件如下所示:
◽ 驾驶状态:未踩油门踏板(滑行)或踩下制动踏板。
◽ 电池状态:电池电量(SOC)低于设定阁值(如50%)且电池温度处于安全范围。
◽ 车速范围:通常大于20 Km/h区间内生效,低速时回收效率较低以避免顿挫感。
并联模式

◽ 能量流:内燃机通过离合器与驱动轴连接,通过机械传动直接驱动车轮;动力电池为主电机(驱动电机)供电,提供额外扭矩支持。呈现"两入一出"能量流趋势,内燃机和主电机(驱动电机)共同将动力传输到驱动轮
该模式适用场景如下:急加速、高速超车或高负荷需求(如爬坡)。
该模式下,双电机拓扑结构实现快速动力耦合,智能电控系统实时调整扭矩分配,避免动力中断。
四、方案优势与局限性
优势:
- 极致能效:发动机专注高效区间(40%-46%热效率),市区工况油耗比燃油车低50%以上。
- 成本控制:全产业链自研(弗迪系供应),系统成本仅为竞品1/3,支持低价策略。
- 驾驶体验:电驱为主带来平顺性,NVH优于传统混动。
局限性:
- 高速油耗劣势:小排量发动机直驱时高转速工况油耗上升,需依赖大电池补能。
- 品控挑战:早期车型存在EV功能受限、刹车异响等问题,反映供应链管理需优化。
- 单档位限制:无法通过多档位进一步优化高速能效,竞品(如长城3DHT)已尝试突破。
五、创新性:技术生态的"涌现式突破"
比亚迪DM-i的颠覆性源于体系化创新而非单点技术:
- 全栈自研生态:从电芯(刀片电池)、电控(IGBT 4.0)到热管理(全温域架构)100%自主,避免"卡脖子"。
- 模块化复用:如EHS系统复用至DM5,CTB电池车身一体化复用刀片电池结构创新。
- 数据驱动迭代:依托440万辆智能车数据,快速优化控制策略(如第五代热管理节能8%-10%)。
六、测试工程师关注点
- 热管理验证:全温域架构需测试-30℃至50℃极端环境下的系统稳定性。
- 模式切换逻辑:重点验证SOC阈值、车速触发条件的平滑性与安全性。
- 耐久性测试:针对单档位离合器、高转速扁线电机进行10万公里级寿命评估。
- 能效标定:通过NEDC/WLTC多工况对比,优化发动机MAP图与电机扭矩分配策略。
结语
比亚迪DM-i通过"以电为主"的架构革新,重新定义了插混技术的边界。其成功不仅在于技术参数领先,更在于构建了从研发到量产的闭环生态。对工程师而言,理解DM-i的构型逻辑与能量管理策略,将为下一代混动系统开发提供关键参考。