01
一、碳化硅晶体材料中的缺陷到底是什么?
碳化硅晶体材料中的缺陷是指在晶体生长、加工或使用过程中出现的不完美结构。
这些缺陷可能表现为晶体内部的裂纹、表面的凹坑、原子排列的错误等。
虽然缺陷看起来微不足道,但它们却可能对晶体的电学、热学和机械性能产生重大影响。
例如:
- 电学性能:缺陷会引入额外的电荷陷阱,影响载流子的迁移率和寿命,从而降低器件的开关速度和功率效率。
- 热学性能:缺陷会导致热导率降低,影响器件的散热性能。
- 机械性能:缺陷会降低晶体的强度和韧性,影响器件的可靠性。
02
二、缺陷是如何分类的?
根据国家标准,碳化硅晶体材料的缺陷主要分为四大类:
晶锭缺陷、衬底缺陷、外延缺陷和工艺缺陷。
接下来,我们将逐一介绍每一类缺陷的典型特征及其产生原因。
(一)晶锭缺陷
晶锭是碳化硅晶体生长的初始阶段,其质量直接影响后续加工和器件性能。晶锭缺陷主要包括以下几种:
-
- 裂纹
-
特征:晶体内部有贯穿型或部分穿透的裂纹,严重时晶体可能碎裂成块。
-
产生原因:在晶体生长、退火或加工过程中,热应力过大或机械应力超过晶体耐受阈值,导致晶体开裂。
-
- 杂晶
-
特征:晶体内部形成的多晶嵌入式生长,与单晶之间存在明显衬度界线。
-
产生原因:生长过程中包裹物或生长条件剧烈波动,导致多晶成核长大。
-
- 边缘多晶
-
特征:多晶附着在晶体边缘,与内部单晶之间存在明显交界线。
-
产生原因:温度场分布不合理导致籽晶边缘升华,或生长初期籽晶处径向温度梯度过小。
-
- 多型
-
特征:晶体中出现6H、15R或3C等异晶型,颜色与4H晶型存在明显差异。
-
产生原因:偏离4H-SiC生长窗口,或生长表面污染物导致异晶型成核生长。
-
- 微管
-
-
特征:微米级直径的物理孔洞,终端延伸至晶体表面,形成小凹坑。
-
产生原因:多型、碳包裹体、硅滴等因素导致局部应变和晶格畸变。
-
(二)衬底缺陷
衬底是外延生长的基础,其质量至关重要。衬底缺陷主要包括以下几种:
-
- 多晶
-
特征:多晶与单晶之间存在明显衬度界线。
-
产生原因:温度场分布不合理或生长条件剧烈波动。
-
- 多型
-
特征:晶体中出现6H、15R或3C等异晶型,颜色与4H晶型存在明显差异。
-
产生原因:偏离4H-SiC生长窗口,或生长表面污染物导致异晶型成核生长。
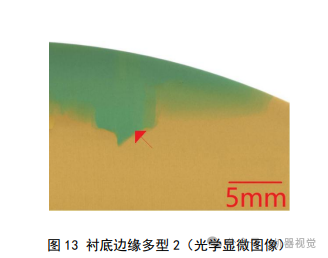
-
- 硅滴包裹体
-
特征:液滴形貌的硅组份夹杂。
-
产生原因:生长过程中硅组分分压过高,形成Si单质颗粒被后续生长的单晶包裹。
-
- 碳包裹体
-
特征:由碳元素组成的固相原子团簇或小颗粒体。
-
产生原因:多晶原料非化学计量比升华或石墨部件腐蚀形成碳颗粒。
-
- 六方空洞
-
特征:六边形的空腔结构。
-
产生原因:籽晶粘接不良导致籽晶背部负生长。
-
- 层错
-
特征:晶面堆叠顺序的错误,分为Shockley型和Frank型。
-
产生原因:机械应力、温度分布不均匀或制备籽晶过程中遗留在其表面上的残余划痕。
-
- 穿透螺位错
-
特征:蚀坑呈六边形。
-
产生原因:籽晶中的TSD遗传至单晶衬底中,或生长过程中引入内应力及应变。
-
- 穿透刃位错
-
特征:蚀坑呈近圆形。
-
产生原因:籽晶中的TED遗传至单晶衬底中,或生长过程中引入内应力及应变。
-
- 基平面位错
-
特征:蚀坑呈贝壳状。
-
产生原因:籽晶中的BPD遗传至单晶衬底中,或生长过程中引入热应力和杂质。
(三)外延缺陷
外延生长是在衬底上形成高质量晶体薄膜的关键步骤。
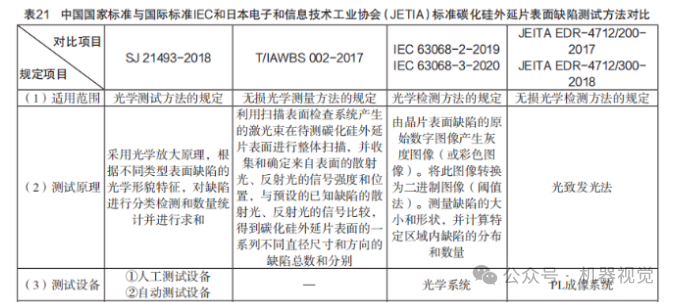
外延缺陷主要包括以下几种:
-
- 掉落颗粒物缺陷
-
特征:孤立出现的大型点状形貌,或以点状颗粒物为头部并伴随出现三角形形貌。
-
产生原因:反应室内颗粒物掉落在衬底或外延层表面。
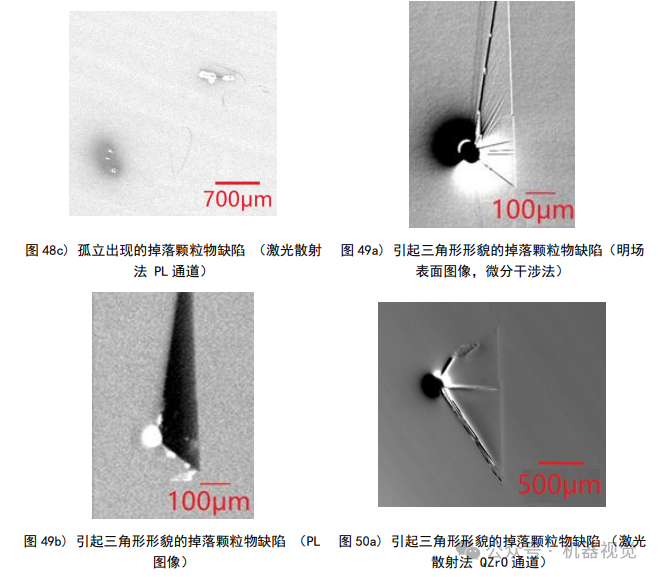
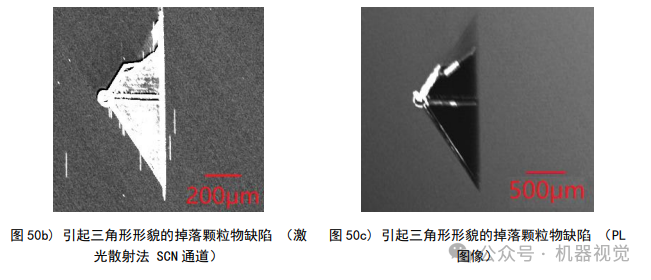

-
- 三角形缺陷
-
特征:从基晶面内延伸到外延层表面的三角形图案。
-
产生原因:掉落颗粒物、乳凸、划痕或TSD影响原子台阶流动。
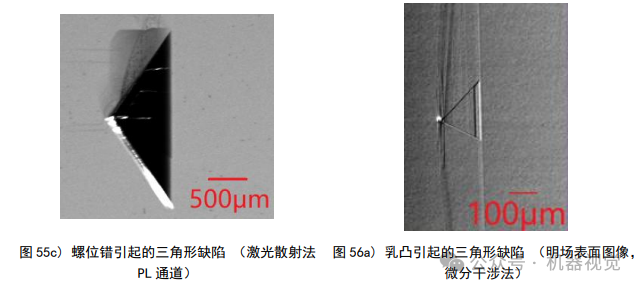
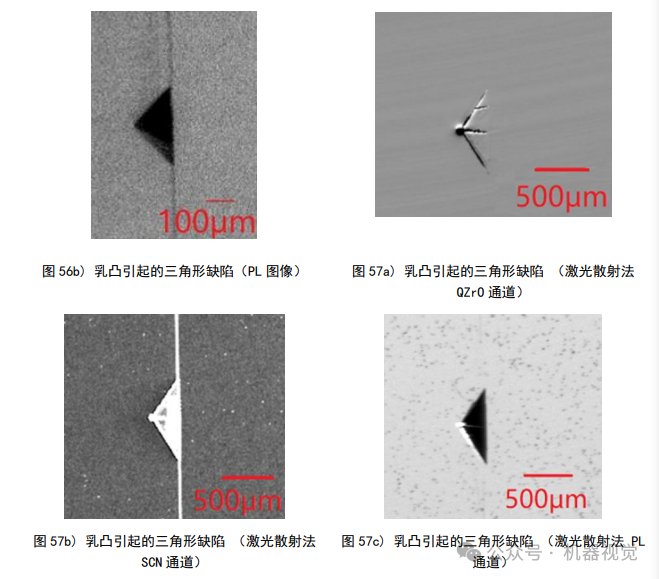
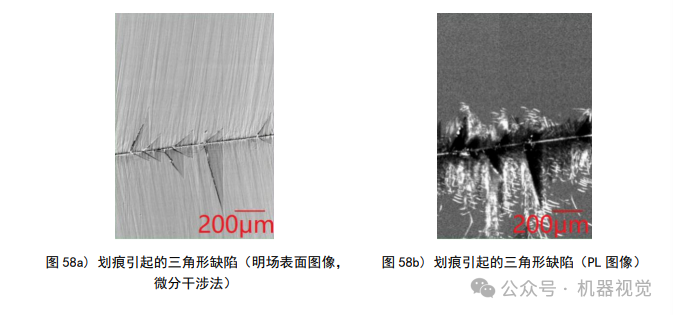
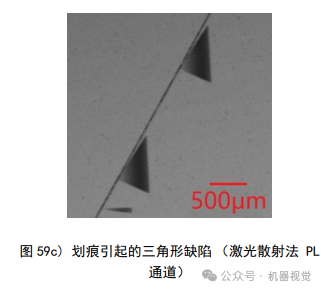
-
- 彗星缺陷
-
特征:明场表面图像和PL图像中呈现彗星状图案。
-
产生原因:外来物影响原子台阶流动,在富硅的外延工艺条件下形成。
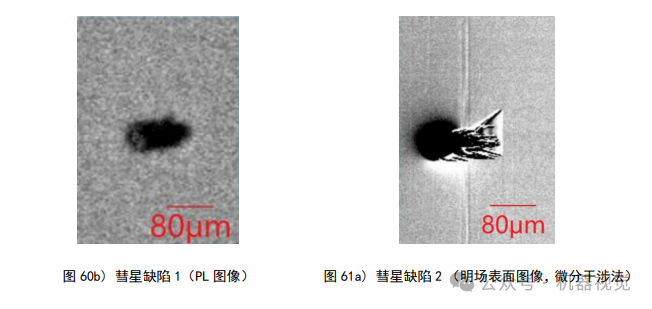
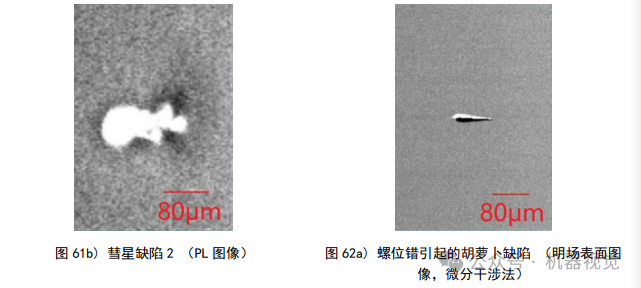
-
- 胡萝卜缺陷
-
-
特征:明场表面图像上呈胡萝卜状图案,PL图像上呈线型图案。
-
产生原因:衬底中的TSD和表面划痕引起。
-
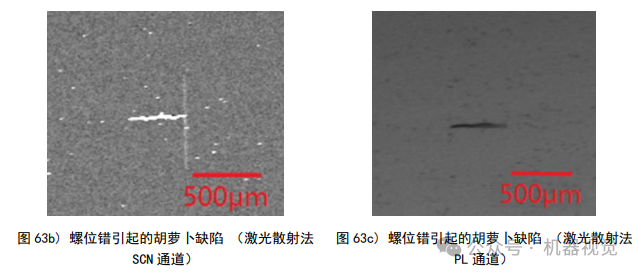
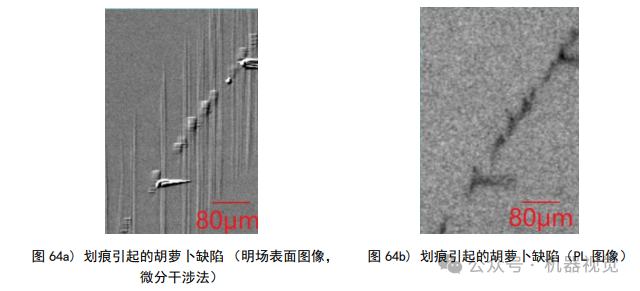
-
- 凹坑
-
特征:小凹陷或小坑状的形貌。
-
产生原因:衬底中的凹坑、TSD和TED贯穿到外延层。
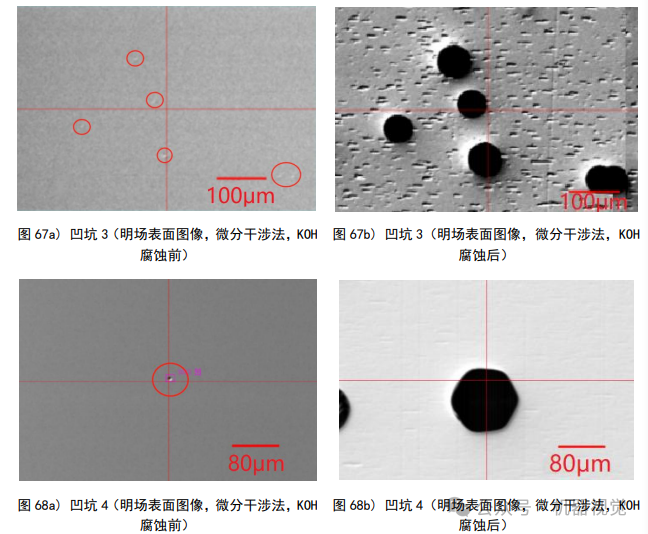
-
- 梯形缺陷
-
特征:明场表面图像上呈梯形状。
-
产生原因:BPD、TED、TSD和划痕周围的位错环影响原子台阶流动。
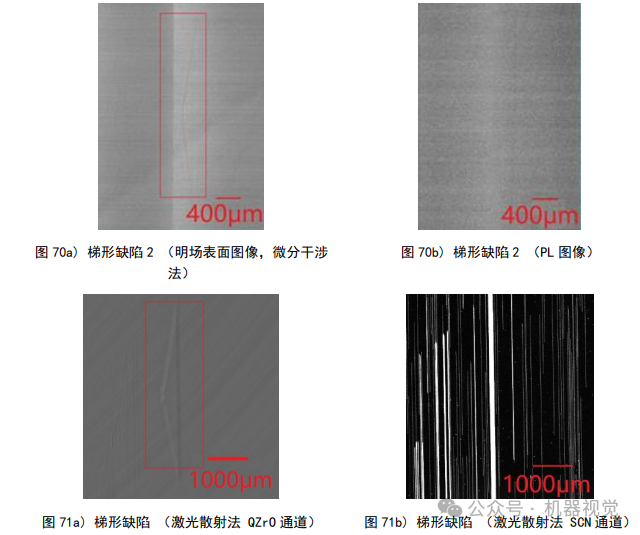
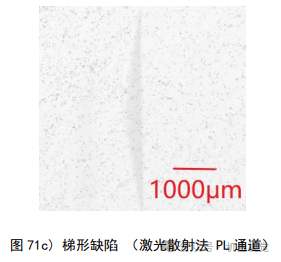
-
- 台阶聚集
-
特征:多个原子台阶汇聚在一起形成的平行线簇。
-
产生原因:衬底结晶缺陷或划痕阻碍原子流动。
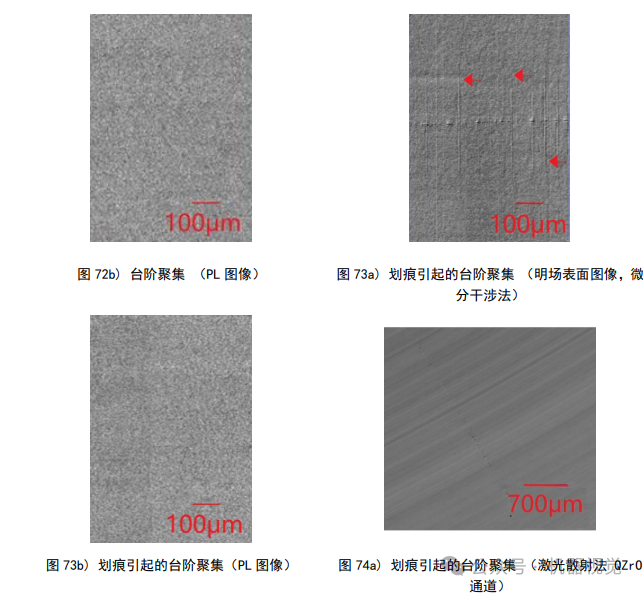
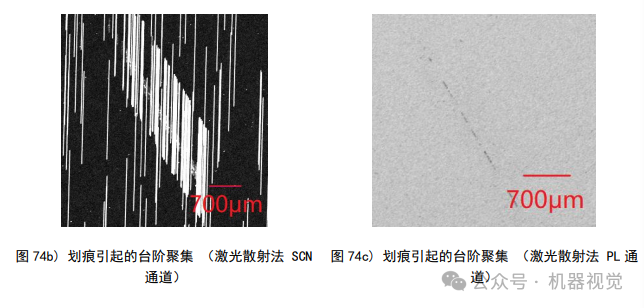
-
- 外延凸起
-
特征:晶片边缘高度凸起。
-
产生原因:晶片边缘应力引起三角形缺陷团簇。
-
- 乳凸
-
特征:表面呈现为凸点或凸起状。
-
产生原因:小尺寸颗粒在外延生长前阶段掉落在晶片表面。
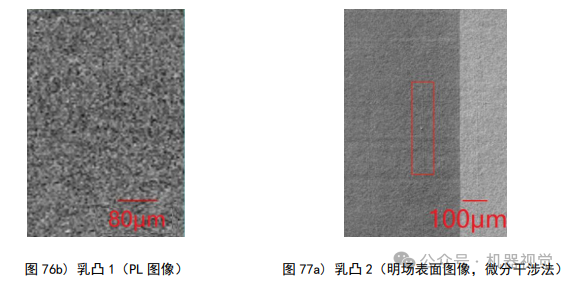
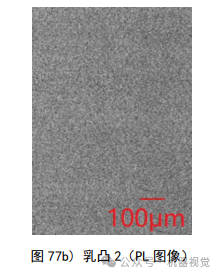
-
- 微管
-
特征:明场表面图像中呈凹坑状,PL图像中呈螺旋纹图案。
-
产生原因:衬底MP贯穿到外延层。
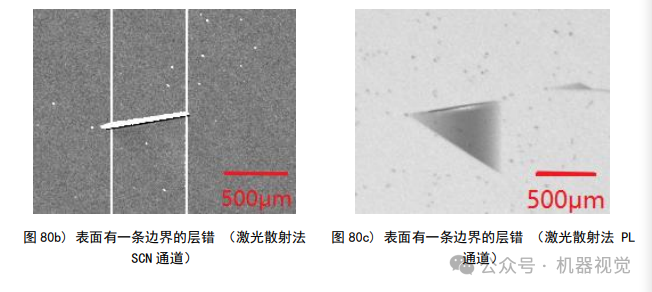
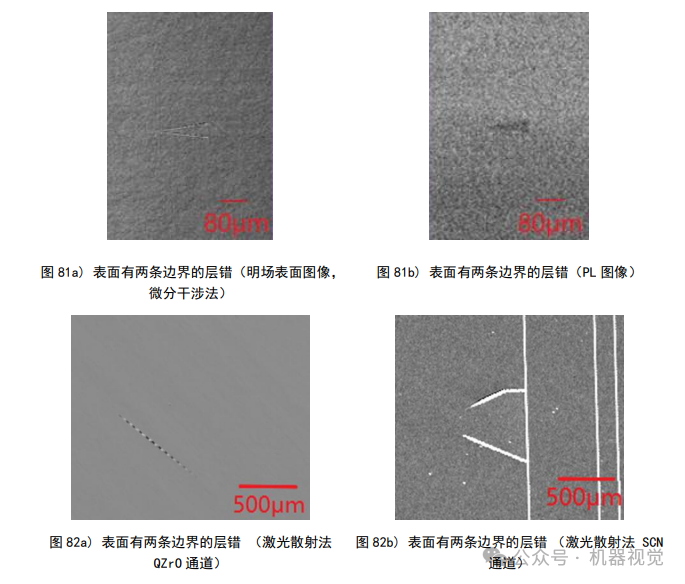
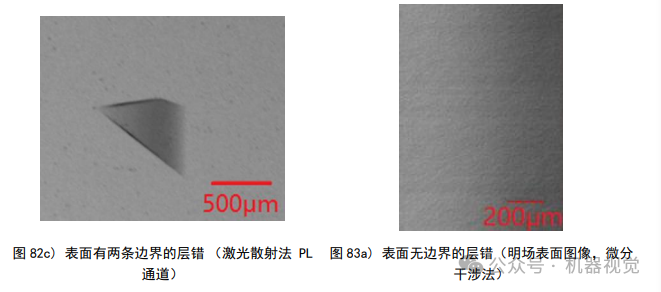
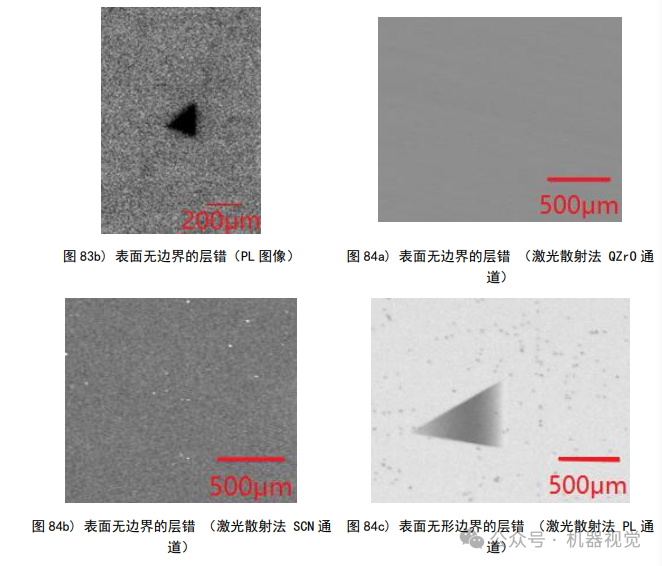
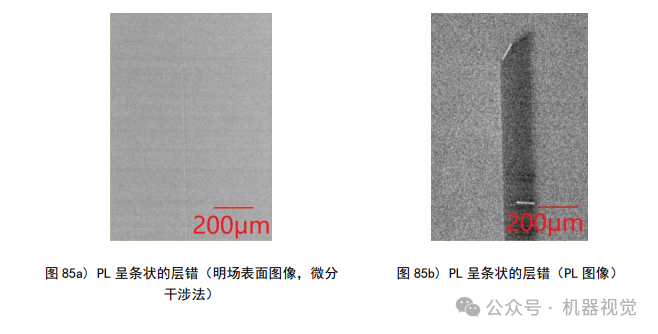
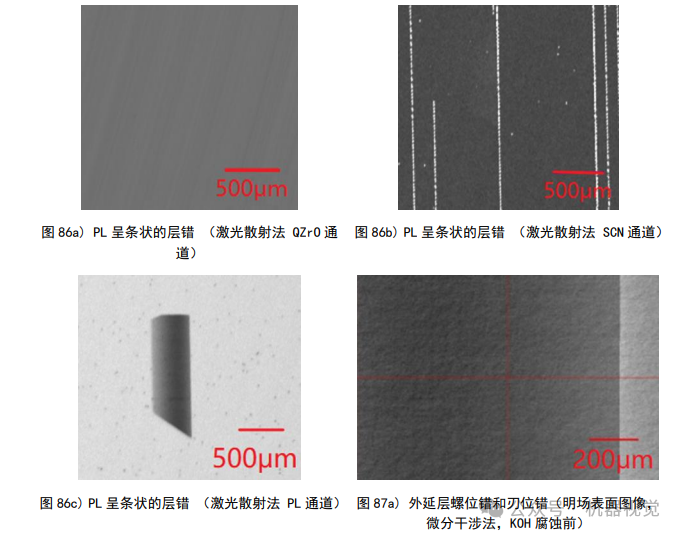
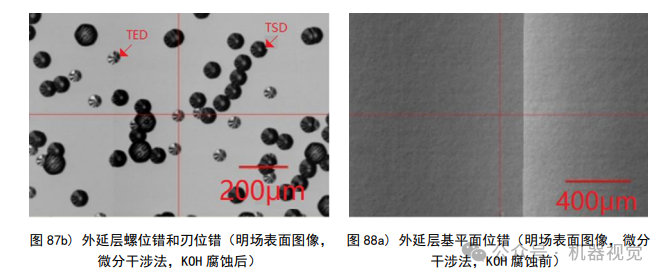
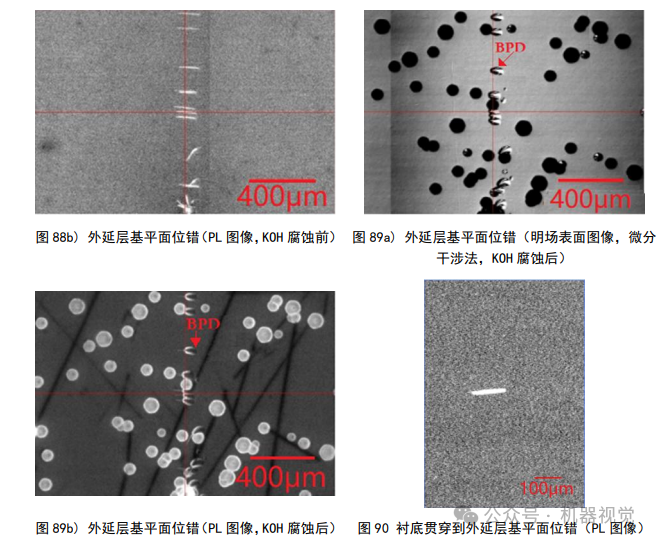
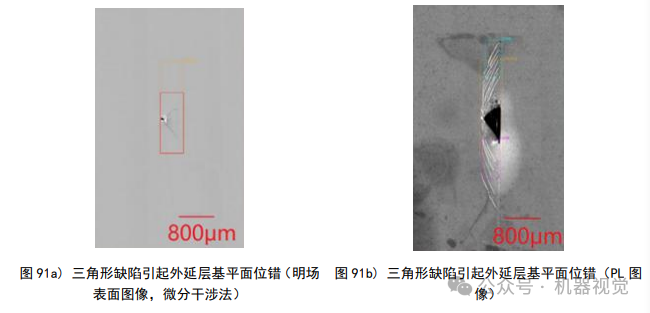
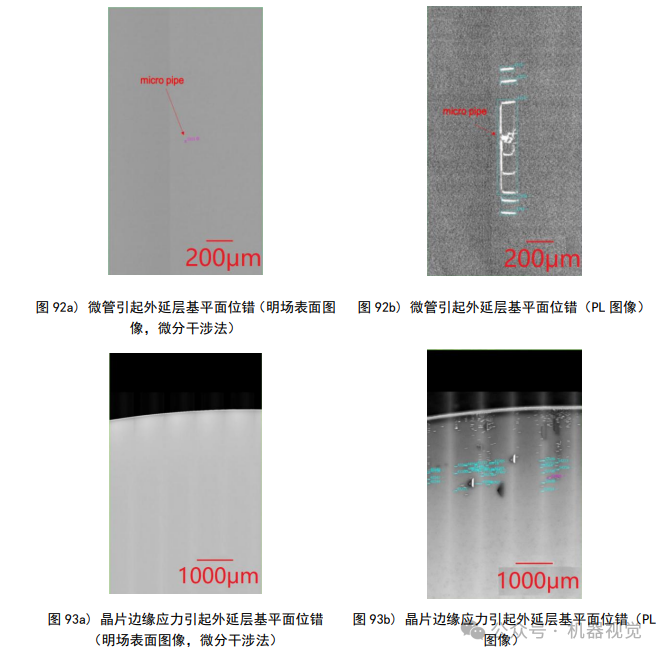
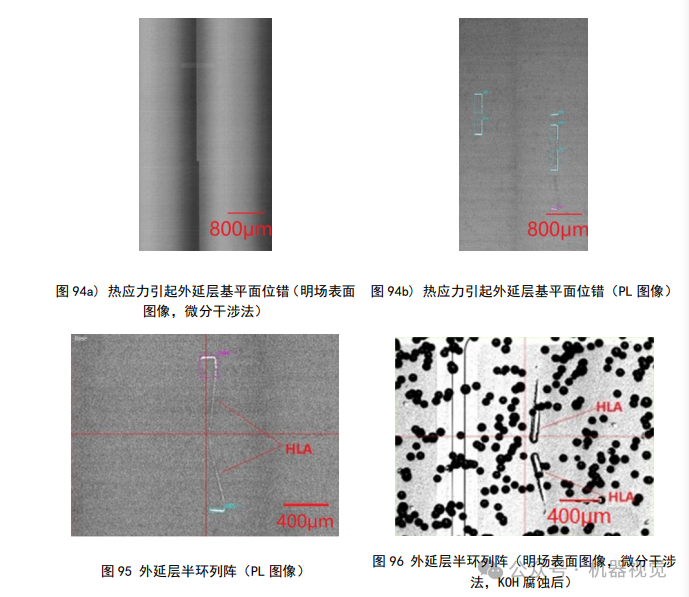
(四)工艺缺陷
在器件制造或材料改性工艺过程中,可能会引入一些深能级中心或非本征结晶缺陷。工艺缺陷主要包括以下几种:
-
- 氧化缺陷
-
特征:高温氧化过程中形成的深能级中心或层错。
-
产生原因:硅和碳原子相分离,形成硅团簇和碳团簇,导致界面碳团簇的形成和位错迁移。
-
- 电应力诱导三角形层错
-
特征:PL图像和EL图像中呈现三角形图案。
-
产生原因:衬底中的BPD在电子空穴复合驱动下分解为两个不全位错并滑移扩展。
-
- 电应力诱导条形层错
- 特征:PL图像和EL图像中呈现条形图案。
- 产生原因:外延层/衬底界面由BPD转化而形成的TED诱导条形层错扩展。
-
- 干法刻蚀缺陷
-
特征:刻蚀工艺在4H-SiC外延层表面和侧壁产生不可逆的结晶缺陷。
-
产生原因:刻蚀工艺在表面和侧壁产生点缺陷或位错环,诱发层错及其扩展。
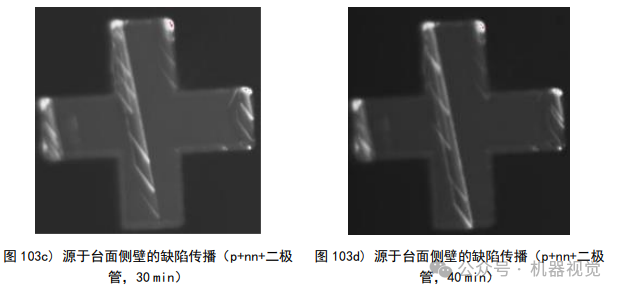