Solder leakage is an important part of electronic manufacturing, and its quality directly affects the subsequent soldering effect and product reliability.As a common problem in the solder paste printing process, solder leakage not only reduces the soldering quality of the product, but also may lead to the failure of the whole product.The following is a brief discussion of the solder leakage phenomenon in the solder paste printing process:
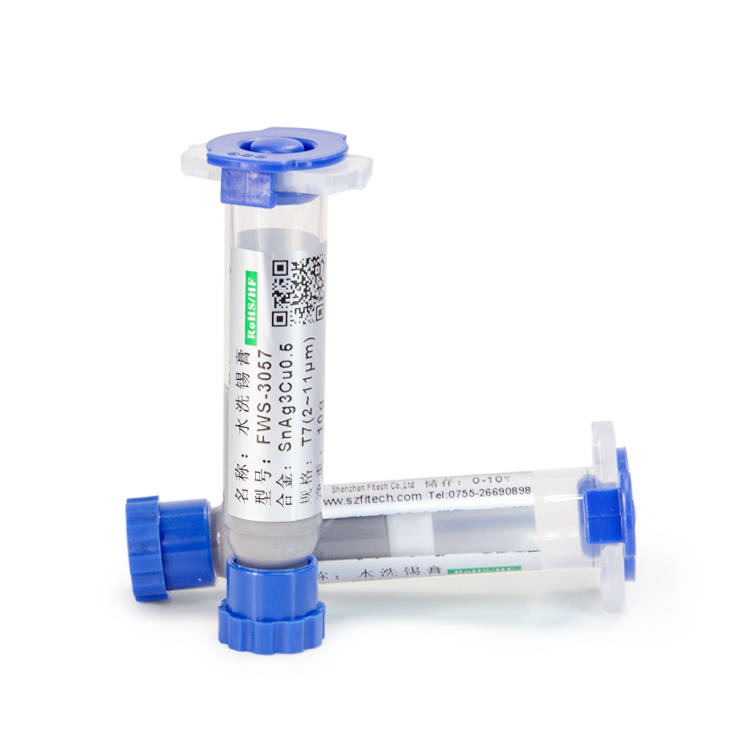
I. The main reasons for leakage welding
Leakage of flux spraying: The flux fails to be evenly sprayed or certain areas are missed, resulting in poor soldering.
Solder paste leakage printing, less tin: the quality of tin paste after continuous printing degradation, stencil opening design is not appropriate, the size of the paste particle size selection is too large or improper printing parameters, resulting in poor tin under the SPI is not detected, and ultimately poor soldering.
Pad oxidation: The oxide layer formed after long time exposure prevents the direct contact between solder and pad as well as wetting and spreading.
Components of the "masking effect": the layout of the component is close or the shape and size of the mask resulting in the solder is difficult to reach the masked area.
Flux "airbag isolation": flux evaporation bubbles formed by the formation of not timely escape, the formation of "airbags" to isolate the solder and the pad.
II. Recommendations for improvement of leakage
- Optimise component layout and pad design
Recommended Layout: As shown in Figure 1-1, lay out the long direction of chip components perpendicular to the transfer direction to reduce shading and improve solder flow.
Pad design: Increase the pad area and optimise the shape to improve soldering quality.
Solder Paste Selection: Select the process window models, long service life of the solder paste, select the appropriate particle size model of the solder paste, to facilitate the consistency of the next tin.
Figure 1-1 Recommended Chip Component Layout
- Welding with turbulent waves
Turbulent wave effect: effectively drive away the flux volatilisation of air bubbles, reducing the "air pocket isolation" effect.
- Improve the component design of blind solder joints
Gap design: As shown in Figure 1-2, make sure there is enough gap between the component mounting base and the PCB board surface for solder to flow in to fill the solder joint.
Temporary Remedy: If the component design is fixed and the height cannot be changed, the component base can be padded by sticking adhesive paper and shims.
Figure 1-2 Artificial Blind Hole Type Weld Joints and Leakage
- Adequate preheating or reduce the amount of solder
Preheating effect: reduce the pad oxide, improve the fluidity of the solder.
Reduce the amount of solder: reduce the number of bubbles formed by flux evaporation, reduce the "airbag isolation" effect.
- Pay attention to the design of the bar and bracket
Design principles: to ensure that the components do not block the heat and tin space, so that the solder can evenly cover the component pins and pads.
III. Conclusions and additions
Solder leakage problem is a key challenge in electronics manufacturing, which directly affects the soldering quality and reliability of products.By implementing the above improvement suggestions, the incidence of solder leakage problems can be significantly reduced.In addition, the following points are additional measures that deserve attention:
Enhance quality control: Regularly calibrate and maintain welding equipment and processes to ensure stability and consistency of the welding process.
Train operators: Improve the skill level and quality awareness of operators to ensure that they are familiar with and adhere strictly to the welding process specifications.
Introduce advanced equipment: Consider introducing more advanced welding equipment and processes, such as laser welding, ultrasonic welding, nitrogen reflow soldering, vacuum reflow soldering, etc., in order to improve welding quality and efficiency.
To sum up, by comprehensively applying a variety of improvement measures and supplementary measures, the leakage welding problem can be solved more effectively and the overall quality and reliability of electronic manufacturing can be enhanced.