在人形机器人仿生架构的构建中,多模态传感器集群与仿生关节矩阵的拓扑融合,正催生第三代具身智能的力学革命。通过分布式触觉薄膜、双目视觉惯性测量单元(200Hz采样率)与肌电模拟传感器的三重耦合,机器人获得了超越人类本体感知的微应变监测能力。但传统工艺在追求微型化的同时,往往难以保证结构强度,制约了人形机器人的发展。而3D打印技术为此提供了全新的解决方案。
通过一体化成型与材料优化,3D打印技术不仅突破了设计限制,还为人形机器人的微型化与轻量化开辟了新路径,其中"三维扫描"技术更是发挥了重要作用,在设计与制造过程中确保了精度与质量的双重提升。
针对微型传感器的制造,金属3D打印工艺能够生产出毫米级的六维力传感器,这种高精度、小体积的传感器在人形机器人中发挥着至关重要的作用。同时,结合蜂窝状复合材料关节的设计,不仅实现了缓冲性能的提升,还有效增强了散热效果。某企业的相关产品已经成功应用于机器人,使得机器人的使用寿命延长了30%,充分证明了3D打印技术在微型传感器制造方面的实力。
3D打印技术在轻量化结构设计同样表现出色。通过拓扑优化算法对机器人骨架进行重构,使用PA12-CF材料进行打印,既减轻了机器人的重量(减重15%),又保持了原有的机械强度。这种轻量化设计不仅降低了机器人的能耗,还提升了其运动灵活性,使得人形机器人在各种应用场景中都能表现出更加出色的性能。
对于客户而言,3D打印技术降低了传感器的制造成本,加速了产品的迭代速度,使得客户能够更快地推出具有竞争力的产品。另一方面,3D打印提升了机器人的运动性能和耐用性,使得客户在使用过程中能够享受到更加稳定、高效的机器人服务。
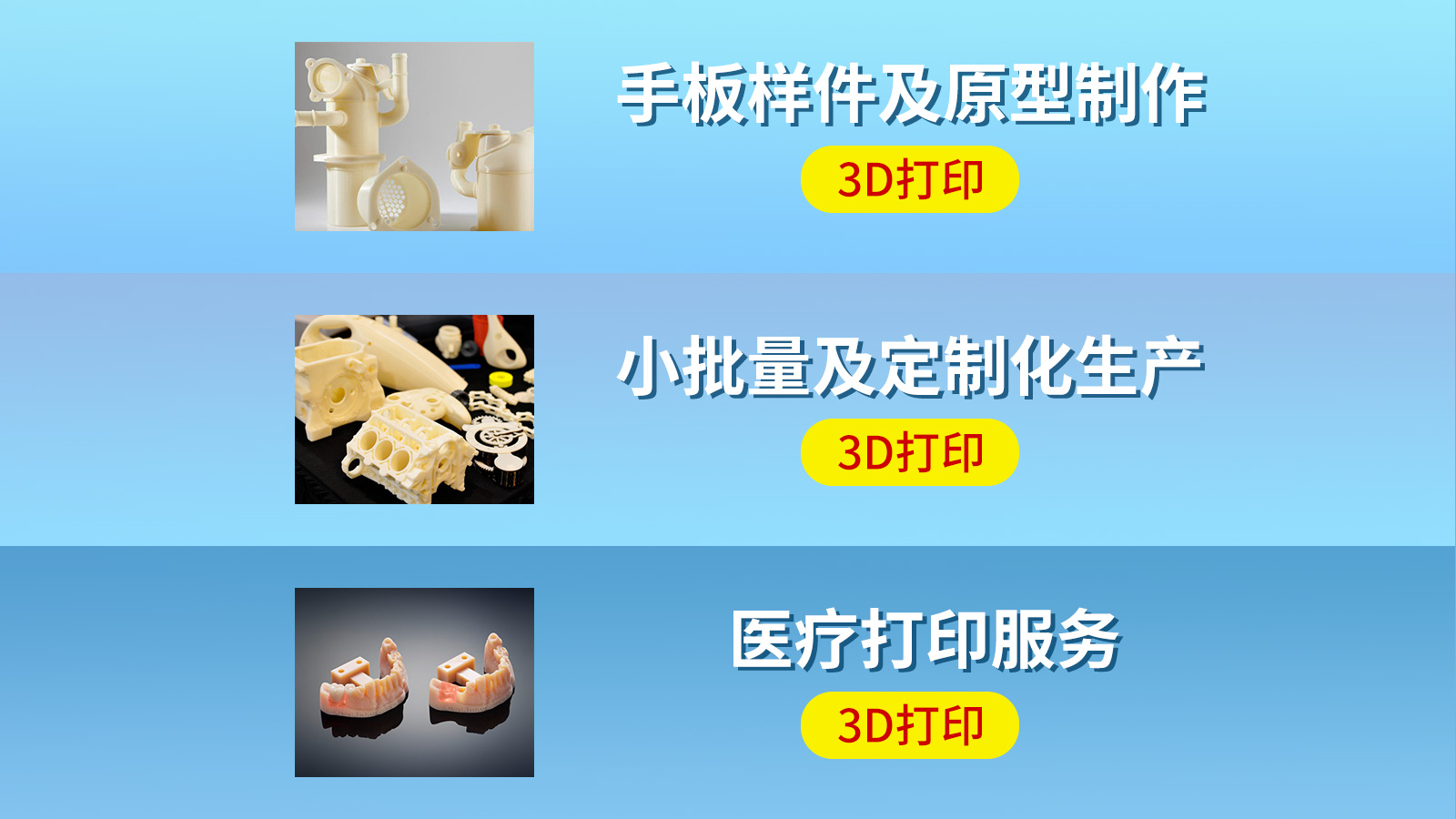