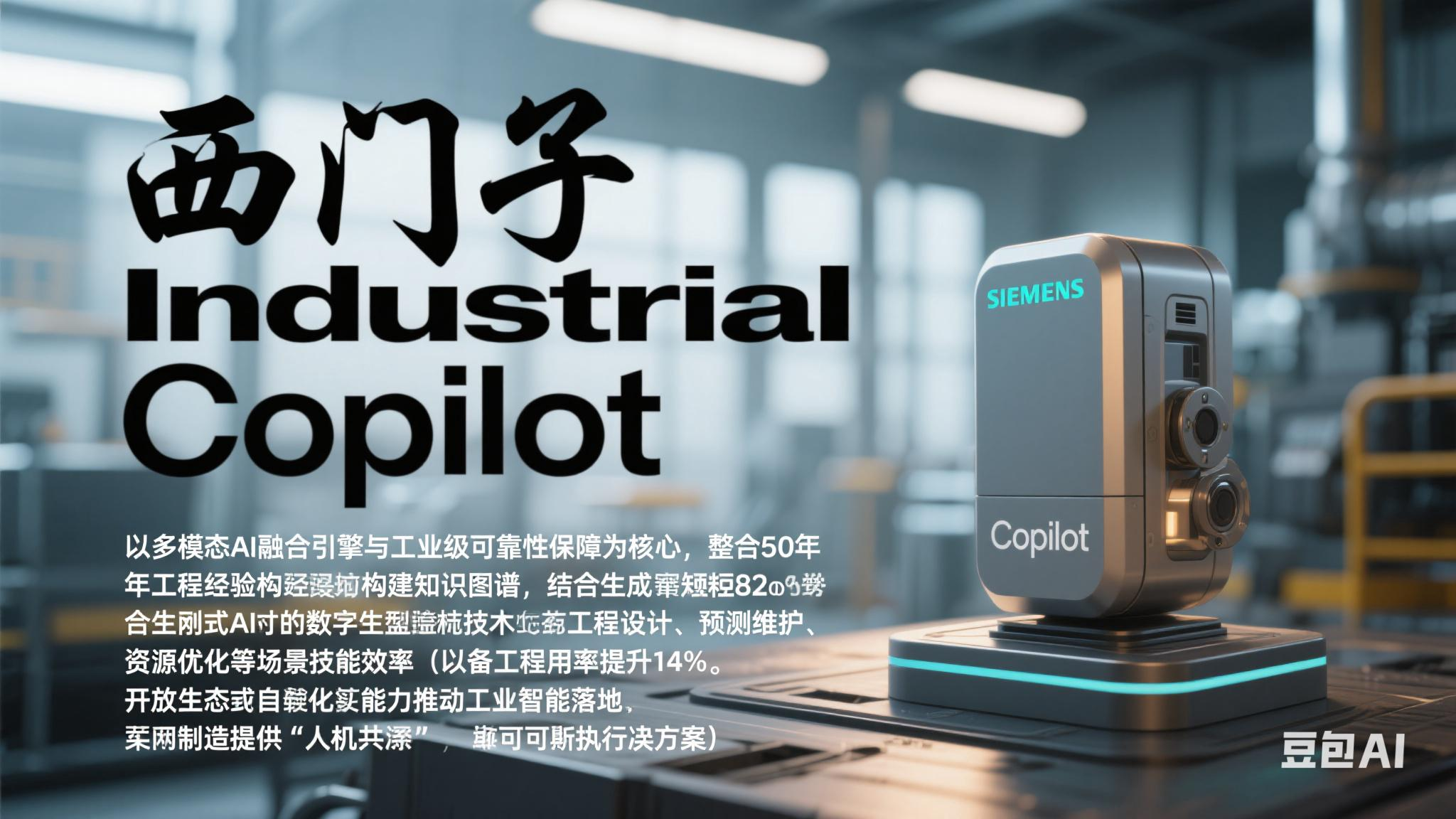
一、技术内核的三重突破
- 多模态融合的工业智能中枢
-
知识工程的数字化积淀:整合西门子百年工业经验,构建包含200万+设备参数、10万+故障案例的动态知识图谱,支持语义推理与跨领域关联分析(如通过电机温度异常反推齿轮箱润滑不足)。生成式AI模块基于DeepSeek-MoE混合专家模型,训练数据覆盖300亿token工业语料,代码生成准确率达99.7%,可自动解析IEC 61131-3标准下的梯形图逻辑。
-
虚实融合的感知系统:移植Vision Pro空间计算技术,开发工业级LiDAR点云处理算法,0.2秒内完成产线环境三维建模,结合数字孪生体实现机器人路径的动态优化(路径规划效率提升40%)。
- 工业级可靠性保障体系
-
数字孪生验证闭环:所有AI决策需通过Plant Simulation数字孪生平台的物理一致性验证,确保代码在真实产线的执行误差<0.01%。某汽车工厂案例中,AI生成的焊接机器人轨迹经孪生验证后,焊点合格率从98.2%提升至99.8%。
-
容错机制的多层防护:设置动态安全边界(如锅炉温度控制±2℃阈值、机械臂运动速度梯度限制),当AI输出超出预设范围时,自动触发"人机共决"流程------3秒内推送预警至现场工程师终端,实现风险的分级响应。
二、场景落地的价值锚点
- 工程设计的范式革命
- 包装产线配置案例:传统模式需5名工程师耗时7天完成PLC编程、HMI设计与虚拟调试;Industrial Copilot通过自然语言指令输入(如"兼容纸箱/泡沫箱,产能100件/分钟"),12分钟内生成包含STL模型、PLC代码、HMI界面的完整工程包,人工校验时间压缩至2小时,工程周期缩短82%,人力成本下降60%。
- 预测性维护的精准突破
- 北京奔驰冲压线实践:部署振动传感器(10kHz采样率)与电流波形分析模型,基于长短时记忆网络(LSTM)构建设备健康度指数,提前48小时预警轴承磨损(准确率92%),维护响应时间从8小时压缩至1.5小时,设备可用率提升14%,年减少非计划停机损失超120万元。
- 能源管理的动态优化
- 南京工厂注塑车间改造:AI实时接入电网数据(5分钟粒度),通过强化学习算法动态调整注塑机参数------低谷时段(23:00-7:00)提升模具预热功率至110%,高峰时段降载至75%,单位能耗成本下降23%,年节省电费超800万元,同时避免电网负荷波动触发的罚款(单月最高曾达35万元)。
三、工程化落地的攻坚细节
- 数据治理的工业级解决方案
-
多协议融合架构:采用OPC UA统一接入200+类设备协议(涵盖Profinet、EtherCAT、Modbus等),开发基于GAN的数据清洗工具,通过生成对抗网络识别机械振动噪声(误信号剔除率99.4%),每日处理15TB工业数据的压缩率达85%,存储成本降低70%。
-
边缘-云端协同架构:部署NVIDIA Jetson AGX Orin边缘计算盒子,实现端侧实时推理(响应时间<50ms),关键数据经联邦学习加密上传云端,模型更新时采用"影子模式"验证,确保热切换延迟<200ms,避免产线停机。
- 人机协作的交互创新
-
自然语言工程化:支持语音指令直接转换为PLC控制代码(如"将传送带速度提高10%"自动生成LAD指令并校验安全边界),集成声学模型过滤车间环境噪声(95dB噪音下识别准确率98%)。
-
AR辅助决策系统:通过Hololens 2呈现三维维修指南,AI自动标注故障部件并叠加动态操作动画(如红色高亮显示需更换的轴承),新手维修效率提升300%,复杂故障处理时间从45分钟缩短至12分钟。
四、生态构建与未来进化
- 开放模型框架的生态扩张
-
多LLM适配体系:支持DeepSeek、GPT-4o、Claude 3等主流模型的一键切换,内置工业级安全中间件,保障军工、医药等行业客户的私有化部署需求(如某航空企业导入涉密工艺知识库,模型推理延迟仅增加15%)。
-
工业AI组件商城:构建开发者生态,第三方可上传预训练模块(如"半导体晶圆缺陷检测模型"),经西门子工业级认证后按调用次数分成(平台抽成15%),首批入驻企业已达200+,覆盖3C、新能源等8大行业。
- 工业元宇宙的深度融合
-
数字线程全贯通:从Industrial Copilot输出的EPLAN图纸可直接导入NX生成数字孪生体,同步至Teamcenter PLM系统形成全生命周期数据链,实现从设计到运维的端到端追溯(变更管理效率提升50%)。
-
虚实联动控制引擎:在元宇宙中完成产线布局优化后,AI自动生成机器人运动学逆解并下发至物理设备,某电池工厂试点中,产线重组时间从72小时缩短至8小时。
- 自进化系统的底层构建
-
联邦学习网络:全球200+工厂数据经加密聚合(隐私计算技术保障数据"可用不可见"),模型每月迭代一次,新增光伏逆变器运维、锂电池注液机控制等细分场景数据,累计优化参数超300万组。
-
因果推理突破:研发工业级因果大模型,通过Do-Calculus算法区分设备故障的因果关系(如识别压力异常是阀门堵塞导致而非传感器漂移),根因分析时间从4小时缩短至20分钟,彻底改变传统故障树分析的局限性。
五、挑战破解与产业启示
- OT/IT融合的技术攻坚
-
协议转换革命:开发支持17种工业协议的智能网关,基于模型驱动架构(MDA)实现配置自动化,传统3天的设备接入周期缩短至20分钟,某食品工厂产线联网效率提升90%。
-
精准时钟同步:采用IEEE 1588v2精密时间协议,结合边缘计算节点的硬件时钟校准,确保AI指令与设备动作的同步误差<1微秒,满足汽车电子焊接等高精度场景需求。
- 工业人才的智能化转型
-
"双料工程师"培养体系:与清华大学共建工业AI微专业,6个月学制融合PLC编程、PyTorch框架、数字孪生技术,首批学员平均薪资提升40%,企业内训成本下降65%。
-
经验数字化工程:通过语音交互系统采集老工程师操作诀窍,AI自动生成结构化知识卡片(累计12万条),构建"专家经验-算法模型-现场执行"的闭环传承,解决技能断层问题。
- 工业安全的主动防御
-
对抗性测试体系:组建专职白帽团队,模拟2000+次攻击场景(如注入高斯噪声污染传感器数据、伪造MES系统工单),通过对抗训练提升模型鲁棒性,某化工企业试点中,异常数据识别率从85%提升至99.2%。
-
区块链审计系统:所有AI决策记录上链存证,满足FDA、GMP等严格合规要求,某医药企业批次追溯时间从72小时缩短至5分钟,同时规避数据篡改风险。
结语:重新定义工业智能的"可执行性"
西门子Industrial Copilot的创新实践,标志着工业AI从"概念验证"迈向"价值兑现"的关键跨越。其技术突破不仅体现在算法精度,更在于对工业场景"可执行性"的深度解构------让AI决策经得起物理世界的误差容忍度考验,让数字工具能够与三十年工龄的老师傅经验无缝衔接,让柔性生产在毫秒级精度与商业效益间找到平衡。当工业设备开始理解"成本""效率""安全"等商业语言,当生产线具备自我优化的"元能力",这场始于技术攻坚的变革,正在重塑工业文明的底层逻辑:不是机器替代人类,而是人机共同创造更智能的生产范式。在这个过程中,每个技术细节都是工业智能化长征的铺路石,而西门子的探索,为全球制造业指明了一条"可落地的未来"。