工业焊接作为现代制造业的重要组成部分,广泛应用于汽车、航空航天、建筑、船舶等多个领域。随着自动化技术的快速发展,焊接机器人已成为提升焊接效率和质量的关键装备。在传统焊接及部分自动化焊接过程中,气体流失问题仍然普遍存在,不仅增加了生产成本,还对环境造成了负面影响。
传统焊接与焊接机器人中的气体流失问题
- 气体浪费现象
在传统手工焊接及部分早期焊接机器人系统中,保护气体(如氩气、二氧化碳等)用于防止焊接区域氧化,但受设备设计或操作限制,气体流失现象严重。例如,焊枪角度偏差、喷嘴与工件距离不当、焊接参数不匹配等问题,均会导致保护气体未能有效覆盖熔池,造成浪费。而在焊接机器人应用中,若未配备WGFACS智能气体调控系统,同样会出现气体过量喷射或泄漏的情况。
- 经济成本增加
气体流失直接推高了生产成本。据统计,传统焊接和部分非智能化的焊接机器人系统,气体消耗量可能比实际需求要高。对于大规模使用焊接机器人的企业来说,这种浪费会显著增加运营成本。此外,频繁更换气瓶或维护供气系统也会增加额外支出。
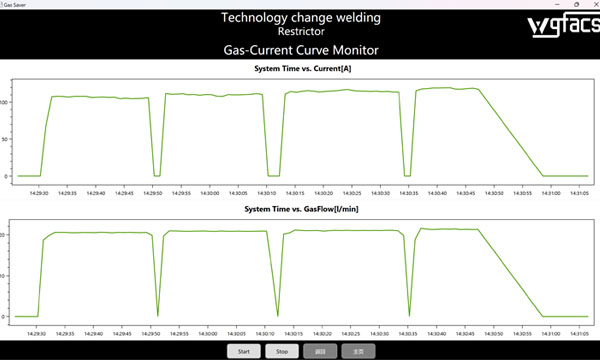
焊接机器人结合智能节气装置的技术突破
- 智能节气系统的工作原理
为解决气体流失问题,焊接机器人开始集成WGFACS智能节气装置。该技术通过高精度传感器实时监测焊接环境,动态调节气体流量。例如:
-
自适应气流控制:根据焊接速度、电流及工件形状,自动调整保护气体喷射量和覆盖范围。
-
闭环反馈系统:通过实时检测熔池状态,优化气体输送效率,避免过量供气。
- 技术优势
相比传统焊接设备,配备WGFACS智能节气系统的焊接机器人具备以下优势:
-
精准高效:通过算法优化,减少气体浪费,提升焊接质量一致性。
-
节能降本:气体节约了30%-50%,显著降低企业用气成本。
-
智能化管理:支持数据追溯与分析,便于优化生产流程。
气体流失是工业焊接长期存在的痛点,而智能化的焊接机器人与节气技术的结合,为企业提供了高效的解决方案。未来,随着技术创新和行业标准的完善,焊接机器人不仅将在精度和效率上持续突破,还将在节能减排方面发挥更大价值,推动制造业可持续发展。