在日常的物料管理业务逻辑中,一物一码是物料管理的基本的业务规则,不管物料从产品开发还是仓库管理,甚至成本核算,都要遵循这个原则,才能保证产品数据的准确性,才具备唯一追溯的可行性。大部分企业都是这种模式,这也是我们非常熟悉的模式。
但在企业某些业务场景中,从不同制造商采购的甚至相同规格参数的物料,接口完全匹配,甚至可以完全替代,但可能质量还存在一些差异,此时对于起来来说,是否进行区分管理不同制造商的物料,如何有利于后续质量的管控是很重要的思考,我们常见的场景包括:
-
针对企业的紧固件等,虽然采购来源于不同制造商,但很多时候在仓库,或者装配制造时并没有区分,即使制造部件有一些差异,很多时候也认为也是完全替代,一般很少出现质量问题,后续也几乎不会出现质量追溯的场景
-
针对电子电气等物料,即使不同企业交付的接口和输出特性完全一致,也具备使用互换,但在某一些特殊场景下,尤其是超额情况下,会出现出差异的特性;因此在出现失效情况下,就需要追溯什么器件在什么情况下引发的问题,需要明确的进行区分
-
在某国内头部的家电企业,针对产品的关键组成部分,虽然也有多供,但是在定义BOM时,尤其是SKU BOM时,组合不同就是不同的SKU,但是对于非关键的组成模块,尤其是大量的电子元件,直接定义了不同制造商供方元件,采购和制造科按需定义和使用,并无追溯的需求
-
在国内某风力发电装备企业,开发时已经充分考虑了替代的管理;在配置订单时,有质量优先和价格优先的选型可对含有多供方的物料进行排序,便于在实际项目中灵活选择(默认价格优先),但是也面临客户指定的场景,可能包含在已经开发的供应商中,也可能不包含,针对不包含的,是否必须开发新的供方,也是困扰企业很久的痛点
针对物料的多供到底该如何管理,尤其面对复杂的应用场景?这里暂无法给出答案,我们再次区分一下IPN/MPN概念,确保我们可以有一个一致的认识:
-
IPN:Internal Part Number,指按企业内部的物料编码进行编码和管理的物料,或者说在企业管理中,忽略了制造商的信息,仅采用企业自己的编码规则确保唯一性和可追溯性的一种定义
-
MPN:Manufacturer part number,指按照制造商的规格型号等信息表达和记录,确保制造商分配的唯一字母数字代码,可用于标识并追溯特定产品或组件,在查询资料时,这里有一个默认的前提,是针对一组相互可替代的物料的约束下
|------|----------|-------------|--------------|
| | 公司内部编码 | A制造商编码 | B制造商编码 |
| 物料编码 | PAT00232 | KD-KL-00322 | CB2N-DCF-032 |
更多有关华为研发管理/IPD、MBSE、PLM、ERP、MES、数据治理、数字样机等方面免费解决方案、资料获取,请见下图,限时优惠。
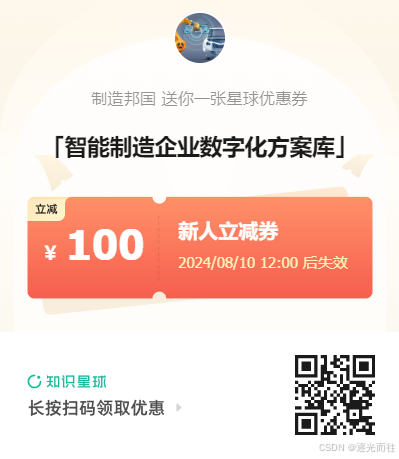
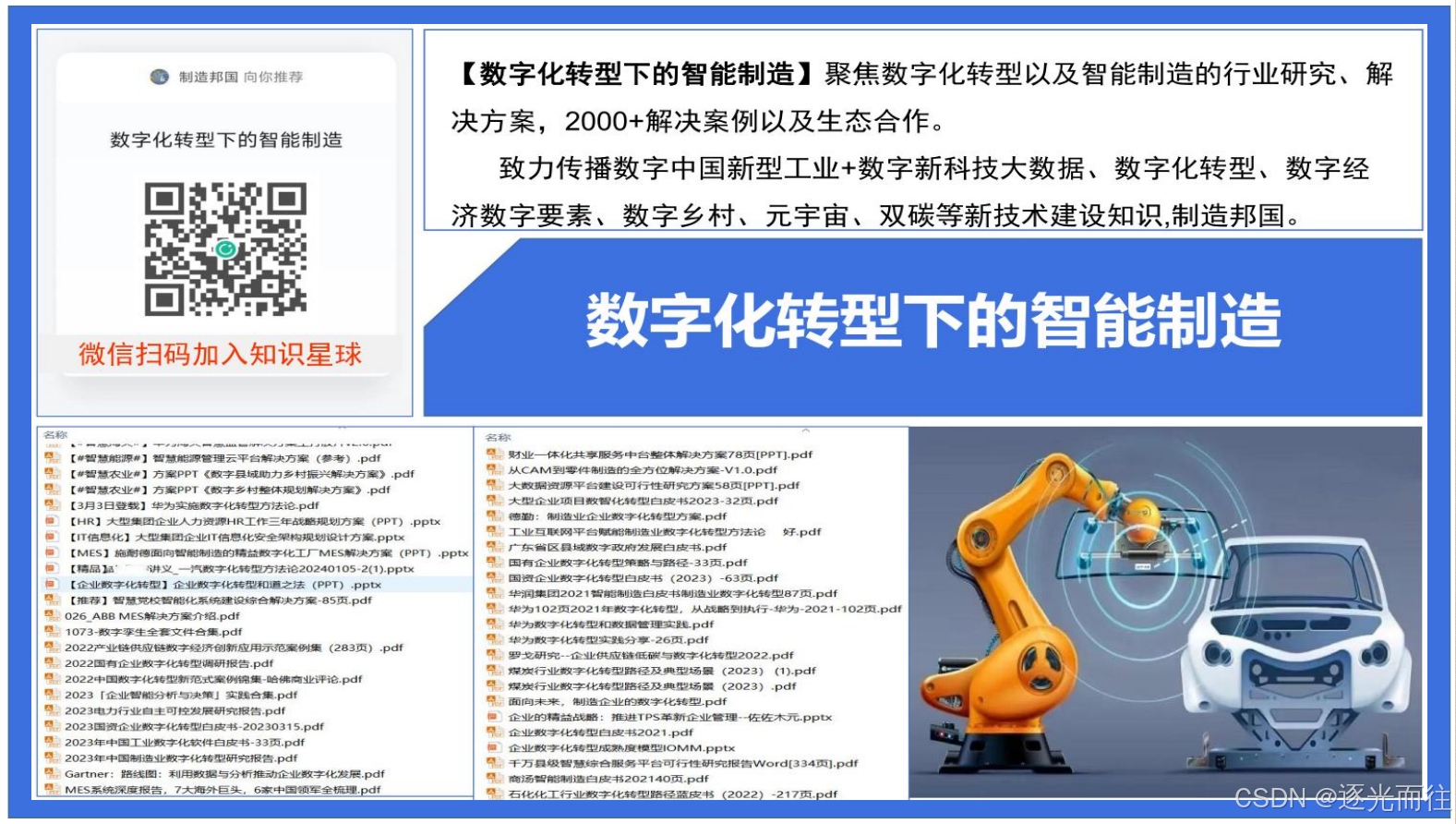
通过上述表达样式可以看到,所谓的IPN就是一物一码,不同的供方物料,对企业来说都有唯一对应的编码;但是对于MPN物料就存在多物一码,初始听着不合理,多个实物使用一个编码,难道不会混乱吗?那对于允许不限制混合使用的场景,是不是就可以?存在即由道理,那么在企业的物料开发管理中,为什么要在IPN定义已经存在的场景下,又在这么多行业和企业出现MPN的定义呢?基于我做的一些分析,将相关内容,尤其站在替代使用的视角,总结以下表单。
|-------------|----------------------------------------------------------------------------------|----------------------------------------------------------------------------------------|
| 分析项目 | MPN | IPN |
| 物料编码 | 单一IPN编码下,可建立MPN组,定义多个MPN,新增供方不需要申请IPN编码 基于供应商的代码和规格型号可确保信息的唯一 | 使用企业内部的编码规则,每一个制造商/方案都是单一IPN编码,新增供方需要申请新的编码 |
| 替代逻辑 | 不同制造商的MPN完全相互替代,优先级一致,可设置替代比例 | 存在完全替代和局部替代场景,若设置替代比例,ERP需要定制开发功能增强 |
| BOM定义 | BOM仅显示IPN编码,不显示MPN(在产品开发时无法指定) | * 方案1(常见):在BOM中仅定义并显示优先级最高的,其余的全部通过替代关系表达 * 方案2:在BOM中并列显示所有的替代关系,但通过启用/禁用的设置定义哪一个替代可使用 |
| 替代应用 | 不同的MPN可根据配置的比例自动计算需求,下游使用不受限制 | 在工单中,使用哪一个替代料需要人工设置,或者默认使用优先级为1的料,若出现库存不足则按优先级顺序消耗库存 |
| 仓库管理 | 采用(Non-inventory managed MPN)时,不单独管理库存,若有特殊指定时,比较难区分(也可以按MPN指定库存,但需要对ERP进行专门的设置) | 每一颗物料都单独存放,很容易区分 |
| 制造商物料禁用 | 除非是物料仅有单一MPN,否则制造商物料的禁用不影响BOM结构,因此这种方式针对成熟且标准化程度较高的物料定义和管理较方便 | 制造商物料即BOM结构上的物料组成,因此禁用时必须对BOM进行变更,使用可替代的物料更换到BOM结构上,否则就会出错 |
| 优势 | * 对于多供场景便于追踪,可在SAP的维护物料采购配额 * 减少重复编码的申请 | * 基于客供,客指等特殊场景物料管理支撑能力较强 * 便于追溯和管理,满足目前用户操作习惯 * 多供方替代不稳定时,使用IPN的替代比较灵活 |
| 挑战 | * 若MPN在实际产品中的装机追溯,对于库存、生产应用等追溯比较麻烦 | * 数据管理和操作维护相对比较麻烦 * 无法记录物料的制造商,无法识别多供方 |
其实对于两种不同的面向多制造商物料管理的方案,我也在一直追寻、思考不同方案的利弊,或者企业选择不同方案的决策关键点,但发现这是一个很难的事情,企业开发的产品不同,对产品组成物料的管控成熟度不同,企业的信息化水平存在差异,都会影响对IPN、MPN方案的选择,没有完美的方案,不过是针对企业面对复杂的物料及多供方甚至延伸到供应链的管理过程中,提供了一种新的思路和方式,不过我的建议如下,仅供参考:
-
物料启用MPN可以通过MPN记录制造商物料开发、验证、变更的场景,但对应IPN物料很难实现这种管理,尤其同一物料不同制造商时
-
若企业新开发物料比较多,并且可能对物料应用产品序列号、产品故障追溯要求比较高时,建议使用IPN而非MPN
-
若企业的IT等信息化成熟度比较低,无法对供应商来料按批次进行追溯,并且延伸到生产上的应用时,建议使用IPN而非MPN
-
若企业大量开发标准类通用类产品,产品比较稳定,组成的物料也比较成熟,则多供管理可使用MPN而非IPN
-
若企业开发的产品在面向市场或用户时,针对订单会指定制造商,则使用MPN的灵活性大于IPN
-
当企业刚开始引入某一新物料时,可使用IPN管理,但随着产品成熟和物料的市场成熟,可考虑改为MPN
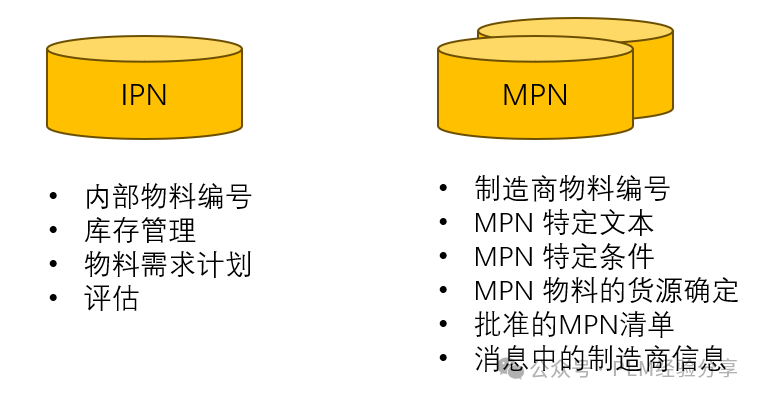
IT系统针对这块是有解决方案的,我查了很多资料,没有相对比较准确的找到IPN的源头,但是针对MPN,大概是来自于SAP的定义,并且在众多行业中被接受和广泛应用,大家也慢慢都接受了这种定义;我前期在实施PTC公司的Windchill PLM时,虽然没有MPN的概念,但是供应商物料其实是相同的作用;在项目实施时,我们也会根据企业的诉求不同,例如不同制造商采用不同制造商部件,那就采用按制造商的模式管理,也将企业的采用IPN替代的管理模式转换成类似MPN的模型结构便于查看和使用。
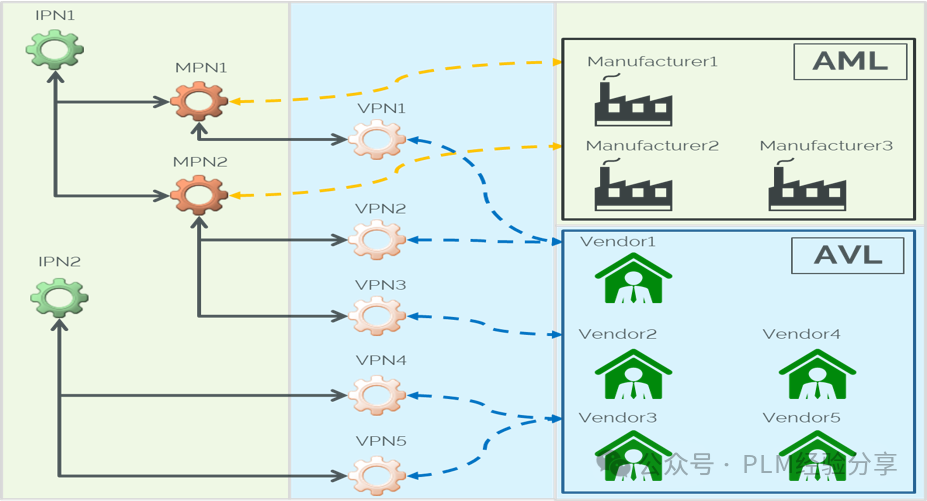
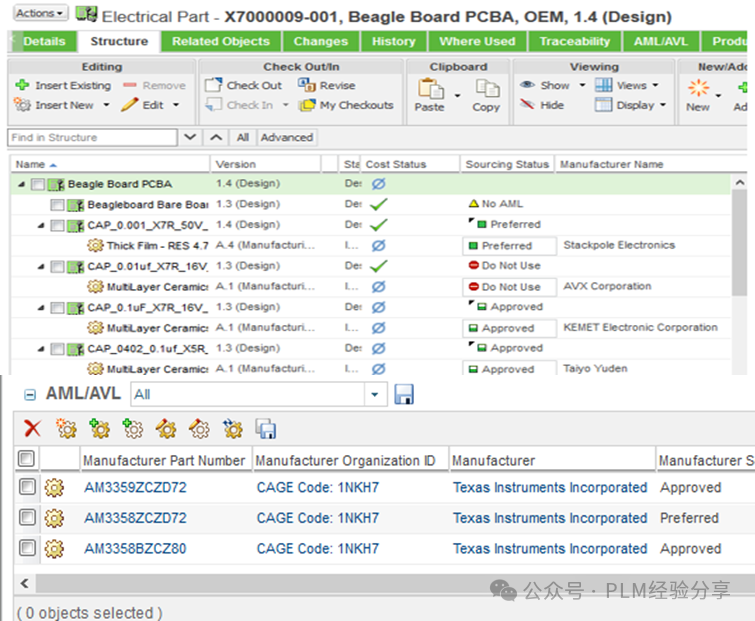
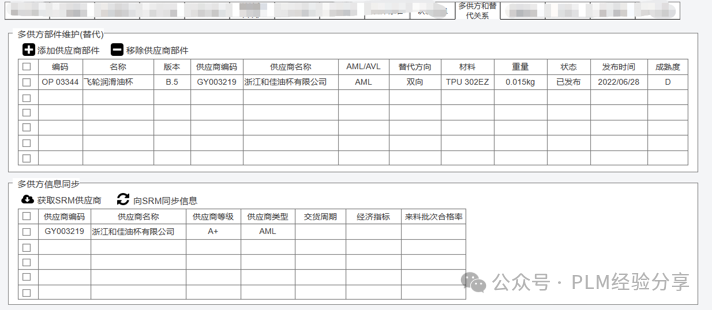
针对SAP系统,其实也可以实现面对MPN的更细致的管理,包括启用针对MPN的库存管理,质量管理等,我也咨询了专家,并且也看了一些对应的操作,发现SAP在这方面功能还是很强大的,好像我了解了几家企业,都没有应用的很深(够用即可)。
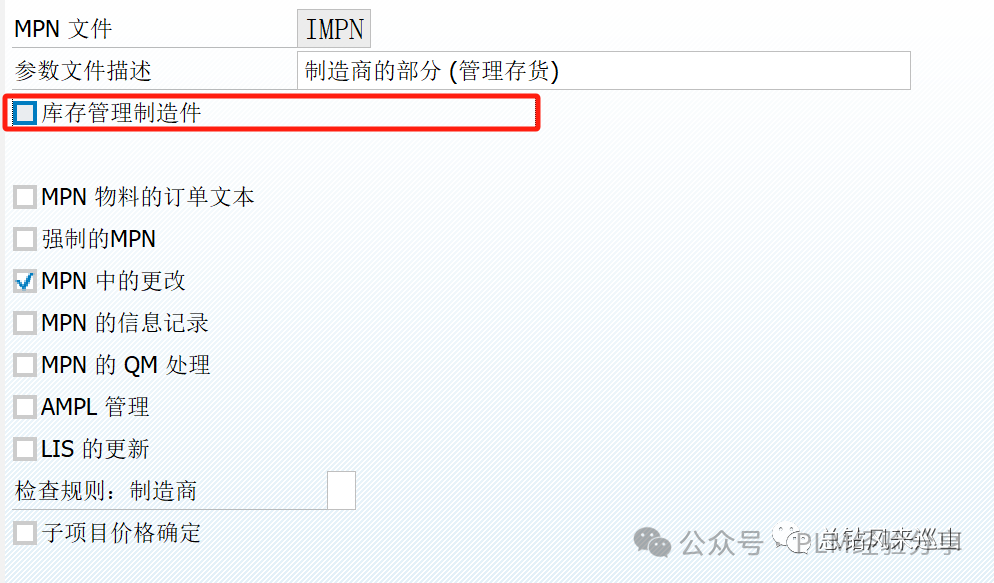