精密铸造和增材制造技术发展,传统接触式测量方法已难以满足复杂曲面、高精度要求的检测需求。手持式三维扫描仪因其便携性、高精度和快速数据采集能力,为铸件尺寸检测、逆向工程、模具修正提供数字化解决方案。
金属铸件的尺寸精度直接影响产品性能和装配效率。传统接触式测量方法存在效率低、数据不完整等局限性,而手持式三维激光扫描技术的出现为铸件检测提供了全新解决方案。这种非接触式测量方式能够在数分钟内获取工件表面完整的三维数据,其测量精度可达0.025mm,完全铸件尺寸标准要求。
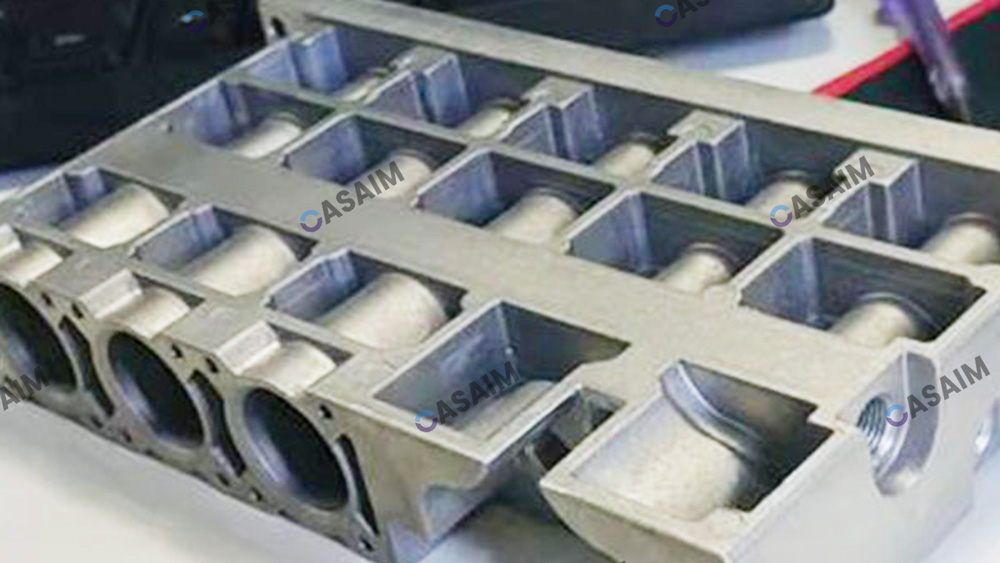
中科米堆CASAIM手持三维扫描技术可实现:非接触式测量,避免损伤铸件表面;单次扫描获取完整三维数据(精度达0.025mm)。
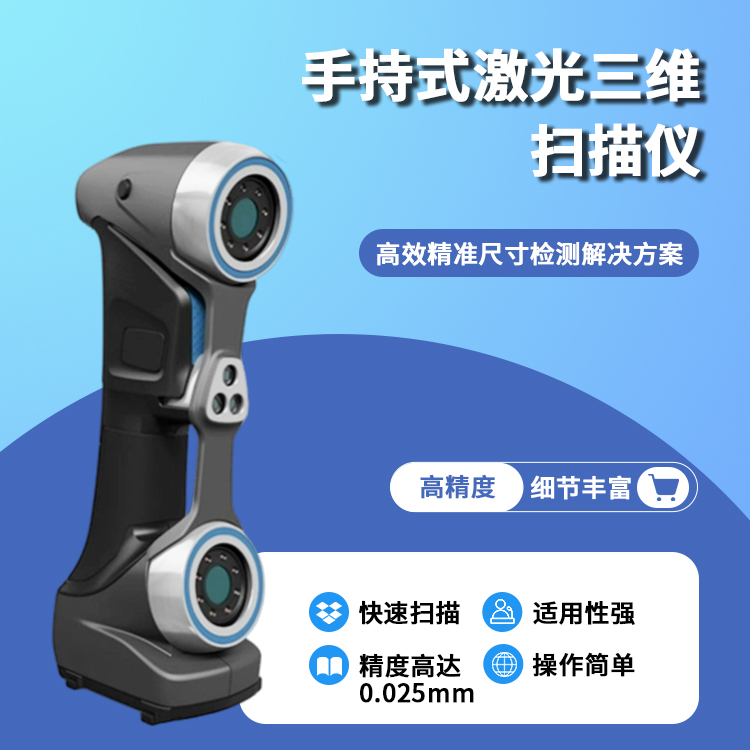
手持式三维激光扫描仪通过发射高速激光束实现对金属铸件的三维测量。设备内置的激光发射器以每秒高达1,800,000次的速率投射激光线到工件表面,通过高精度CMOS传感器接收反射光信号,根据激光三角测距原理计算每个点的空间坐标。扫描过程中,仪器通过参考工件表面粘贴的定位标记点,实时追踪扫描头的位置和姿态变化,确保多角度扫描数据的自动对齐。这种激光扫描方式不受环境光干扰,对金属材料表面的适应性更强,尤其适合铸造车间复杂的作业环境。
扫描完成后,专业软件可自动对齐扫描数据与CAD模型,生成直观的色谱偏差图。工程师能够快速识别出加工误差超出公差范围的区域,特别是对分型线错位、拔模角度偏差等铸件典型缺陷的检测灵敏度显著提升。
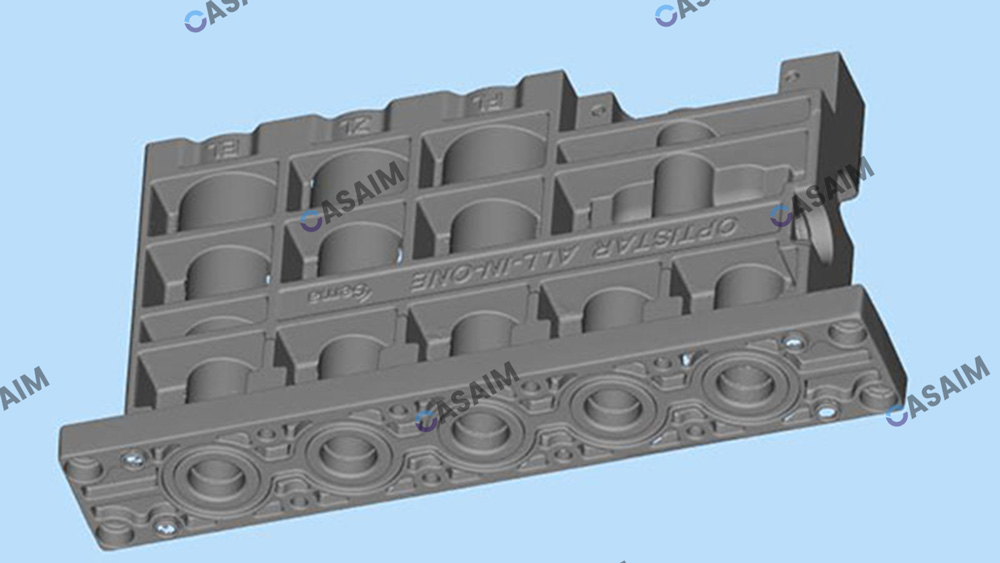
某重型机械制造商在采用了我们手持式三维扫描仪设备后,铸件返工率下降42%,新产品试制周期缩短35%。
随着工业4.0的推进,三维扫描数据正成为数字化工厂的重要工具。扫描仪获取的高密度点云可用于逆向工程、模具修复、虚拟装配等多个环节。部分生产制造企业已实现扫描数据与MES系统的直连,建立实时质量监控体系。