系列文章目录
1.元件基础
2.电路设计
3.PCB设计
4.元件焊接
5.板子调试
6.程序设计
7.算法学习
8.编写exe
9.检测标准
10.项目举例
11.职业规划
文章目录
- 1、什么是SMT和SMD
- 2、表面贴装技术的优势是什么?
- 3、通孔和表面贴装技术之间的区别是什么?
- 4、焊料桥接或电气桥接
- 5、焊点不足或电气开路
- 6、焊锡球化
- 7、立碑效应
- 8、不湿润或去湿润
- 9、焊锡球
- 10、填充物不足和焊料不足
- 11、冷焊点或颗粒状焊点
表面贴装技术不是一个零缺陷的焊接工艺。在这篇文章中,我们将研究表面贴装技术(SMT)中导致PCB失败的原因,并试图找出避免这些错误的方法。减少此类缺陷是提供高效PCB组装服务的关键。
在我们了解SMT组装中的错误之前,让我们先了解一下SMT的基本情况。
1、什么是SMT和SMD
SMT贴片指的是在PCB基础上进行加工的系列工艺流程的简称,PCB(Printed Circuit Board)为印刷电路板。SMT是表面组装技术(表面贴装技术)(Surface Mounted Technology的缩写),是电子组装行业里最流行的一种技术和工艺。
SMD:它是Surface Mounted Devices的缩写,意为:表面贴装器件,它是SMT(Surface Mount Technology)元器件中的一种。在电子线路板生产的初级阶段,过孔装配完全由人工来完成。首批自动化机器推出后,它们可放置一些简单的引脚元件,但是复杂的元件仍需要手工放置方可进行回流焊。表面组装元件(Surface Mounted components)主要有矩形片式元件、圆柱形片式元件、复合片式元件、异形片式元件。
2、表面贴装技术的优势是什么?
与通孔安装相比,SMT有几个优点。表面贴装技术使自动化变得容易,并使电路板上的元件密度更高。它还可以实现更高的电路速度,同时提供更好的高频性能。
3、通孔和表面贴装技术之间的区别是什么?
表面贴装技术和通孔技术之间有几个区别。主要的区别是围绕成本、自动化、电路板空间和元件密度。通孔元件的制造成本比表面贴装元件高,不适合自动化。与SMT相比,通孔技术在电路板空间和元件密度方面也有更高的限制。
表面贴装技术的故障排除
4、焊料桥接或电气桥接
焊料桥接是指焊料横跨两个不应电气连接的导体,并导致电气短路。这些短路导致了电路的故障。
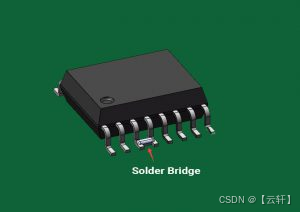
①、原因:
各种各样的原因可以说明桥接的原因;然而,最广泛认可的原因是锡膏印刷过程中的一个问题。印刷过程中钢网与PCB焊盘匹配出现在偏差。
锡膏体积太大同样也会造成桥接。当钢网孔径与焊盘的比例过高时,可能会发生这种情况。
锡膏的突然坍落(Slump)也同样会促使桥接的发生。
②、什么是坍落度(slumps)
坍落度(slumps)通常是做坍落度试验测定拌合物的流动性,并辅以直观经验评定粘聚性和保水性。坍落度是用一个量化指标来衡量其程度的高低,用于判断锡膏能否正常进行。
不正确的锡膏金属与助焊剂重量比例会导致坍落(Slump)。高温和湿润度同样可以促使锡膏坍落(Slump)。
回流焊曲线也同样会增加桥接。我们知道,回流过程的目的是融化焊膏中的粉末颗粒。与此同时,它还会润湿被连接的表面,最后,使焊料凝固,形成牢固的冶金结合。剖面图可以分解成四个区域 - 预热、浸泡、回流和冷却区。
如果预热区的斜率过慢,就会造成桥接。零件与焊膏的接触可能会使沉积物发生偏移,使焊膏发生桥接。延长浸泡时间会给锡膏输入更多的热量,导致锡膏热坍落(Slump)现象。
放置不准确会进一步缩小焊盘之间的间隙,从而增加了桥接的机会。太多的元件放置压力会把锡膏从焊盘中挤出来。
③、解决方案:
适当的应用需要一个适当的焊膏金属和助焊剂重量比。换句话说,焊膏不能有坍落(Slump)现象。例如,通常可分配的焊锡膏的金属含量为85-87%。如果我们将其用于细间距的表面贴装印刷,这一比例会出现坍坍落(Slump)。通常情况下,90%的金属是,或者至少应该用于网板印刷焊膏的应用。
适当的回流焊曲线也是非常重要的。
应适当注意网板孔径与焊盘的对准,除非你使用自动印刷机对准。
确保点上的压力和元件放置的准确性。
将钢网孔径的尺寸减少10%。否则,网板的厚度也可以减少,这将减少锡膏的沉积量。
5、焊点不足或电气开路
当两个电气连接点分离时,或PCB上的某个区域中断了电路上的预期设计,则被称为电气开路。
①、原因:
表面贴装工艺的焊膏印刷阶段对这种缺陷的影响最大。
焊点上的焊料不足将导致电路开路。如果锡膏堵塞在网板的孔隙中,就会发生这种情况。
即使焊料量足够,如果在回流过程中没有接触到引线和焊盘,也会发生开路。这被称为元件引线共面性。
开孔也可能是PCB制造过程本身造成的结果。
②、解决方案:
首先,最重要的解决方案是纠正纵横比。纵横比被定义为开孔宽度与网板厚度的比率。锡膏堵塞孔径的原因可能是长宽比太小。
在制造过程中,极端的环境条件是一个严格的禁区。通过控制环境来避免焊膏污染。
关于共面性的调查在解决电气开孔问题时也非常重要。
必须与PCB供应商检查制造情况。
6、焊锡球化
从形成接头的主体中分离出来的非常微小的球形焊料颗粒的发展。这是免清洗工艺的一个基本问题,因为大量的焊球会在两个相邻的引线之间形成假桥,从而给电路带来功能问题。在水溶性工艺中,焊球并不是一个很大的问题,因为它们在清洁过程中会定期被清除。
①、原因:
焊膏的湿气污染是产生焊锡球的主要原因之一。湿气在回流过程中饱和,留下焊锡球。
缺乏适当的回流曲线也会导致焊锡球。快速的预热率不能提供足够的时间让溶剂逐渐蒸发。
焊膏中的焊粉上有过多的氧化物也会形成焊球。
焊球也可能是由于焊膏印刷对位不良造成的,在这种情况下,焊膏被印刷在焊接掩膜上而不是焊盘上。
在印刷过程中,网板底面的锡膏被涂抹也是一个原因。
②、解决方案:
建议使用较粗的粉末尺寸,因为细小的粉末尺寸有更多的氧化物,并且更容易坍塌。
应根据焊膏选择回流焊工艺。
应避免焊膏与水分和湿度的相互作用。
检查使用的最小印刷压力。
在进行回流焊之前,应持续验证印刷对准。
确保正确和经常清洗网板底部。
7、立碑效应
立碑,有时也被称为曼哈顿效应,是指部分或全部从焊盘上拉下来的芯片元件,在只有一端被焊接的情况下变成了垂直位置。这是在回流焊接过程中力的不平衡造成的。元件站在一端,就像从死里复活一样。因此,它看起来像墓地里的墓碑。实际上,它是一个失效的PCB设计,有一个开放的电路。
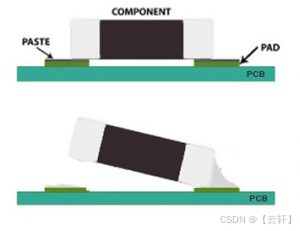
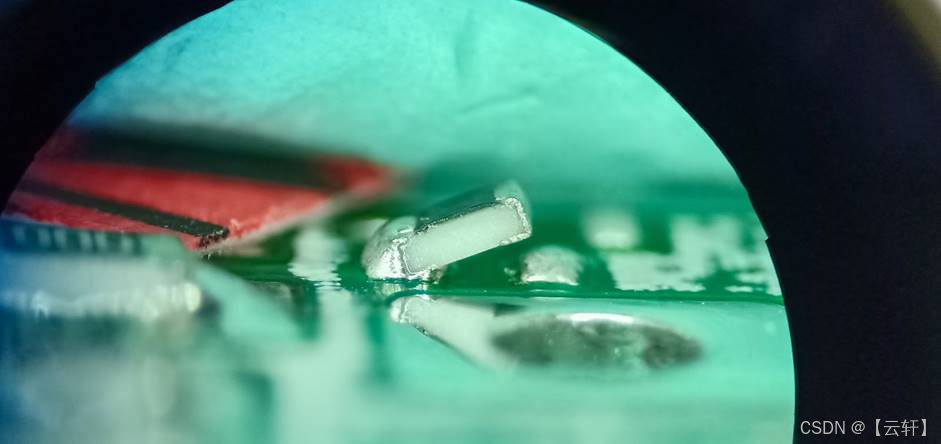
①、原因:
不均匀的加热会造成元件端子间的差异。更准确地说,如果热量分布不均匀,焊料会以不同的速度融化。因此,一边在另一边之前回流,导致另一边的引线直立起来。
不平等的散热器,即地平面,如果存在于PCB层内,可能会把热量从焊盘上吸走。
有时由于温度和湿度对焊膏的影响,在回流过程中,焊膏的力量不足以将元件固定在原位。
在回流操作期间和之后的过度移动可能会导致元件错位,从而导致墓碑效应。
在回流焊之前,元件在焊盘上的不平等放置会导致不平衡的焊料力。
②、解决方案:
元件主体必须至少覆盖两个焊盘的50%,以避免焊接力的不平衡。
确保高的元件放置精度。
建议保持较高的预热温度,以便在回流时两端的差值较小。
尽量减少移动,在SMT组装过程中,尽量减少回流焊时的移动。
尽量减少暴露在极端环境中,如高温或潮湿。
延长浸泡区有助于在锡膏达到熔融状态之前平衡两个焊盘的润湿力。
8、不湿润或去湿润
在焊点中,液态焊料没有与至少一个部件紧密粘连的情况。一种情况是,表面接触了液态焊料,但部分或没有焊料紧贴在上面。
①、原因:
PCB表面处理不佳可能是主要原因之一。假设基本金属是可见的,通常这更难焊接,因此会出现不湿润。
这也可能是由于在回流过程中浸泡时间过长。导致焊接前的助焊剂耗尽。
可能是在回流过程中,热量不足,因此,助焊剂没有得到适当的激活温度。
②、解决方案:
需要适应更好的金属表面处理质量,如更高的耐温OSP或ENIG。
减少在回流阶段前的总轮廓时间。
为给定的焊接任务提供适当的助焊剂。
9、焊锡球
位于离散元件附近的较大焊球的形成,彼此之间的距离非常小。这种变形就像焊球,但它是离散的,因为这些焊珠紧贴着离散的元件,而不是多引线的小玩意。
①、原因:
通常情况下,这种问题是由于沉积了过量的焊锡膏造成的。
有时在预热阶段,会有助焊剂放气,这可能会推翻锡膏的凝聚力。
过大的元件放置压力也可能是一个问题。这可以将沉积的焊膏推到焊接掩模上。因此,不能再融合到接头中。
②、解决方案:
减少网板厚度或减少孔径尺寸。在焊珠出现的一侧,减少10%应该可以解决这个问题。
减少元件取放的压力。
10、填充物不足和焊料不足
在印刷站沉积的锡膏量远远小于网板开口设计,或者在回流后,没有足够的焊料在元件引线处形成圆角。
①、原因:
网板孔有时会被干涸的锡膏堵住。这是导致该问题的主要原因之一。
在印刷周期中,在刮刀片的整个长度上施加足够的压力是非常重要的。这将确保网板被擦拭得很干净。太大的压力会导致浆料被挖出,特别是在较大的垫子上,这可能导致缺陷。
由于刮刀速度太高,浆料没有滚入孔道。刮刀的行进速度决定了焊膏滚入钢网孔隙和PCB焊盘上的可用时间。
当焊膏的粘度和/或金属含量太低时。
②、解决方案:
可以将大的开口分割成小的孔径,并检查刮刀的压力是否过大。
网板必须定期清洗,并检查锡膏是否过期或干燥。另外,应确保有足够的纸板支撑。
刮刀速度过快也是不可取的,这一点也应加以控制。
11、冷焊点或颗粒状焊点
有些焊点有时会表现出润湿性差,在焊接后拥有灰色、多孔的外观。它可以通过合金的深色、不反光、粗糙的表面来识别,而这些表面应该是明亮和有光泽的。
①、原因:
列出的主要原因之一是焊料吸收的热量不足。这种情况的发生是由于存在回流焊料的热量不足。
很多时候,在SMT焊接过程中,助焊剂似乎没有能力完成任务。这可能是由于在进行焊接之前,对元件和或PCB焊盘的清洁不够。焊剂溶液中太多的杂质也会导致这种缺陷。
②、解决方案:
最高回流温度应足够高,以便材料被彻底回流。
在回流期间或紧接着回流之后,组件不应经历任何形式的移动。
必须进行合金分析,以检查是否有污染物。
随着PCB的小型化,与PCB制造有关的问题也在增加。随着PCB上使用更小的元件,需要对焊接过程进行更严格的控制。减少SMT中的常见错误是提高SMT制造效率的一个重要步骤,从而实现更有效的PCB组装服务。