智能制造概念的普及和技术的发展,工业设备的预测性维护已成为提升生产效率、降低运营成本的关键。本文将介绍一种基于ARM架构的端侧无线边缘计算盒子在工业设备预测性维护中的实践应用,并通过具体案例展示其如何帮助企业实现更高效的设备管理。
工业设备预测性维护的重要性
传统的设备维护方式多为定期检查或事后维修,这种方式不仅耗费大量的人力物力,而且难以及时发现潜在问题,容易导致意外停机和生产中断。相比之下,预测性维护通过对设备运行数据的实时监控和分析,可以在故障发生前预判并采取措施,从而有效减少停机时间,延长设备使用寿命。
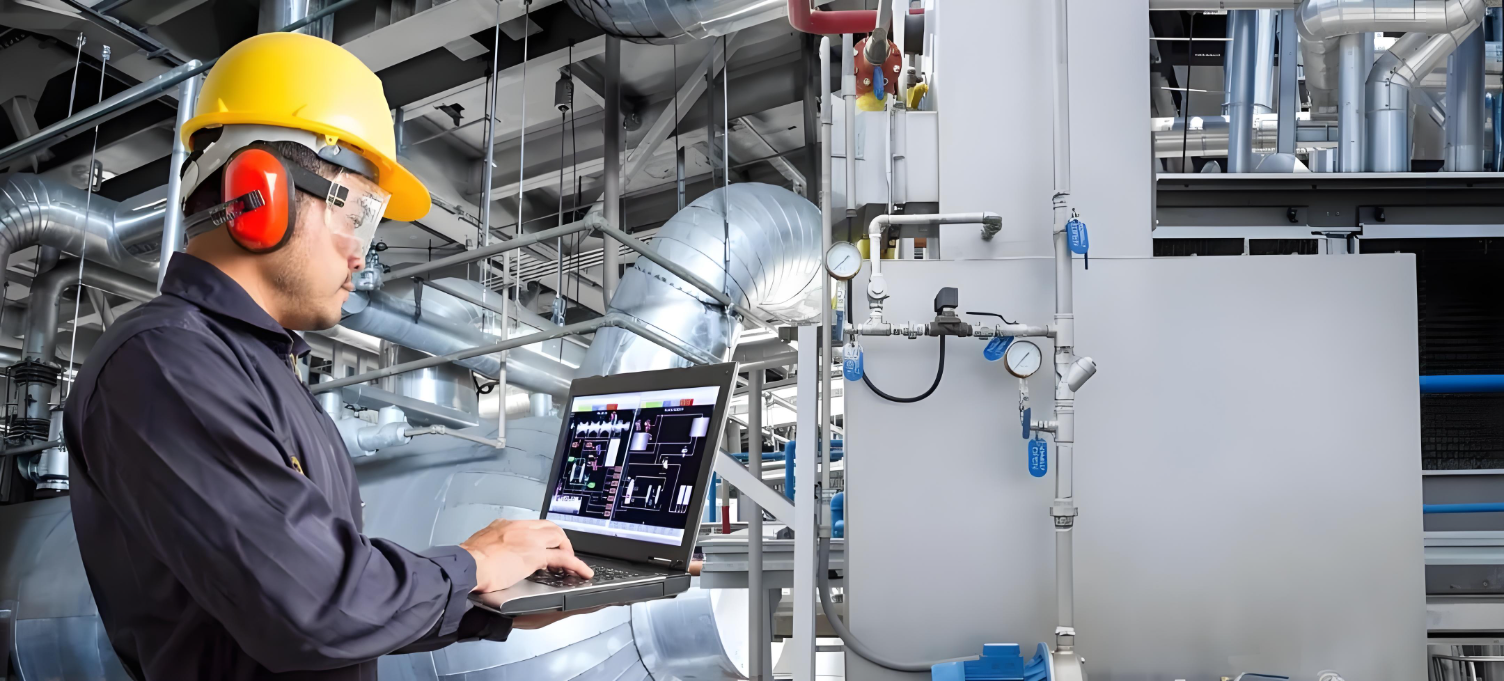
ARM边缘盒子的技术特点
基于ARM架构的边缘计算盒子(如采用全志T507处理器的产品)具有低功耗、高性能以及良好的可扩展性等优点。它能够直接部署于工业现场,连接各种传感器和执行器,采集设备的振动、温度、压力等多种参数,并利用内置的机器学习算法对这些数据进行本地处理。此外,这类盒子通常支持Wi-Fi、蓝牙等多种无线通信技术,便于快速搭建物联网(IoT)环境,无需复杂的布线工程。
预测性维护的工作流程
- 数据采集:边缘计算盒子通过连接到设备上的传感器网络,持续收集设备工作状态的相关信息。
- 数据分析与模型训练:利用本地计算资源,盒子可以执行初步的数据清洗、特征提取等操作,并根据历史数据训练出适合特定设备的故障预测模型。
- 异常检测与预警:一旦检测到偏离正常范围的数据模式,系统会立即发出警报通知相关人员,同时提供详细的诊断报告帮助技术人员迅速定位问题所在。
- 远程维护与优化:借助无线通信功能,运维人员可以通过移动终端随时随地访问设备数据,实施远程调试和维护工作。
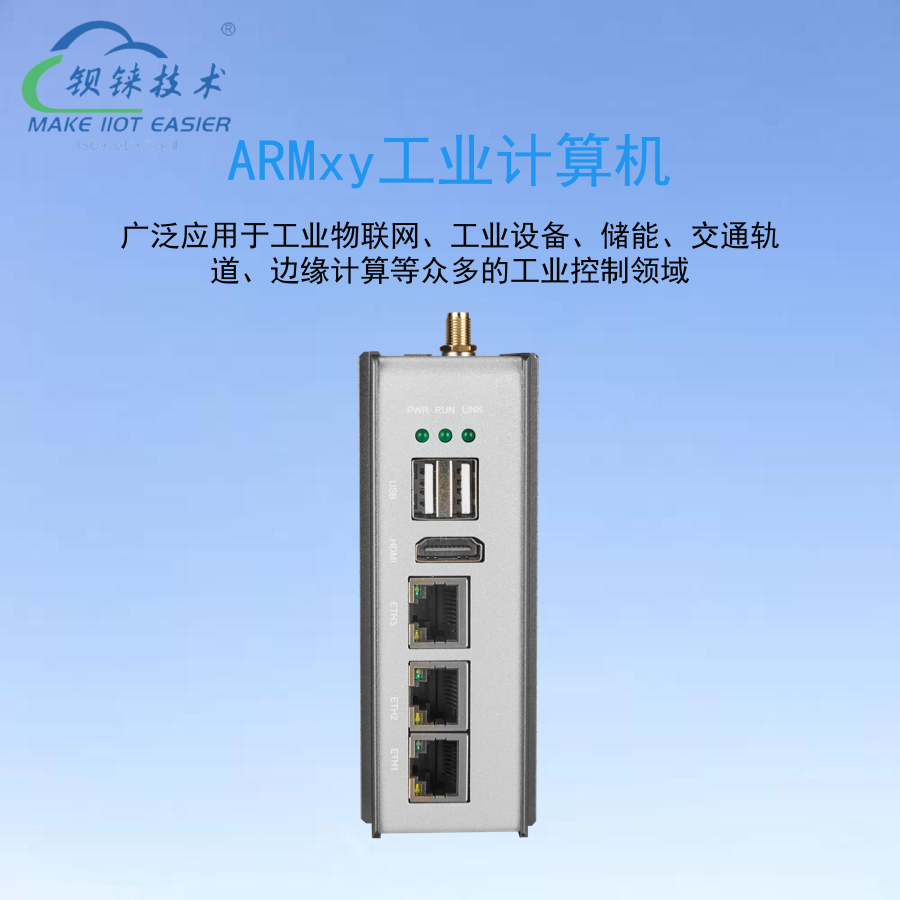
实际案例分析
一家汽车制造企业在其生产线上的关键设备上安装了基于ARM架构的端侧无线边缘计算盒子。经过几个月的运行,该系统成功预测了几起可能影响生产的严重故障,提前进行了预防性维护,避免了非计划停机造成的巨大损失。据统计,实施预测性维护方案后,企业的设备可用率提高了约15%,维修成本降低了近20%。
基于ARM架构的端侧无线边缘计算盒子为工业设备预测性维护提供了强有力的支持。它不仅简化了系统的部署过程,降低了硬件成本,还显著提升了设备管理的智能化水平。未来,随着更多先进技术的应用,我们有理由相信,这种解决方案将在推动制造业向数字化、智能化转型方面发挥更加重要的作用。