一、 设计要点
1.轻量化:
核心目标: 最大程度减轻结构重量,提升有效载荷能力、续航时间、飞行速度和机动性。
实现手段: 选用高比强度/比刚度材料(碳纤维复合材料、航空铝合金、钛合金、工程塑料)、拓扑优化、尺寸优化、拓扑优化、中空/夹层结构设计、功能集成。
2.强度与刚度:
强度: 结构必须能承受飞行中遇到的各种极限载荷而不发生永久变形或断裂。
刚度: 结构需有足够刚度抵抗变形,保证气动外形精度、避免气动弹性问题、保证传感器的安装精度和稳定性、确保飞控系统稳定。
3.气动效率:
外形优化: 设计流线型外形,减少阻力。
表面质量: 保证结构表面光滑、连续,减少寄生阻力。
布局设计: 优化机翼、尾翼、起落架、传感器支架等部件的布局,减少相互干扰和气动遮蔽。
4.功能性集成:
空间布局: 合理规划内部空间,紧凑、高效地容纳电池��、飞控、电机电调、通信设备、任务载荷(、线缆、散热系统等。
结构多功能化: 设计时考虑结构同时作为设备安装平台、线缆通道、散热器等。
模块化设计: 便于快速更换任务模块、电池、维修部件(如旋翼臂)。
5.可靠性与安全性:
冗余设计: 对关键结构考虑冗余路径。
损伤容限: 结构在出现小损伤(如小裂纹)后仍能安全完成飞行任务。
失效模式分析: 预测结构可能的失效模式(断裂、屈曲、疲劳),并在设计中规避或缓解。
适坠性: 对某些应用(如物流、载人无人机),需考虑在意外坠毁时保护载荷或人员的安全。
6.可制造性与成本:
工艺选择: 设计与所选制造工艺相匹配,避免过于复杂或难以加工的几何形状。
公差控制: 合理设定公差,保证装配精度和性能,同时控制制造成本。
装配性: 设计应便于快速、准确地装配和后续维护。
材料成本: 在性能满足要求的前提下,选择成本效益高的材料和工艺。
7.环境适应性:
耐候性: 考虑在温度、湿度、盐雾、紫外线辐射等环境因素下的性能稳定性和耐久性(材料选择、防护涂层)。
抗振性: 隔离或抑制电机、旋翼产生的振动,保护精密电子设备和传感器。
电磁兼容: 结构设计(如碳纤维的导电性)可能影响天线性能,需考虑电磁屏蔽或天线布局优化。
二、 设计难点
1.轻量化与强度/刚度的矛盾:
这是最核心的难点。追求极致轻量化往往意味着削弱结构,如何找到最优平衡点极具挑战。过度减重可能导致结构脆弱,刚度不足引发振动或气动弹性问题;过于保守则牺牲性能。
2.多学科耦合优化:
结构与气动耦合: 结构变形影响气动性能,气动载荷又作用于结构(气动弹性问题)。
结构与飞控耦合: 结构动力学特性(模态、刚度分布)直接影响飞控系统的稳定性和响应性能。
结构与载荷/任务耦合: 不同任务载荷对结构布局和强度提出不同要求。
同时优化结构、气动、控制、热管理等多学科目标非常复杂。
3.复杂载荷预测与验证:
载荷不确定性: 飞行环境复杂多变(突风、湍流、非标准机动、意外碰撞),精确预测所有可能的极限载荷组合困难。
动态载荷: 振动、冲击载荷(如着陆、发射)的分析和测试难度大。
疲劳载荷谱: 建立准确的长期服役疲劳载荷谱并进行寿命预测是难点。
4.复合材料结构的复杂性:
设计自由度大但复杂: 铺层方向、顺序、厚度、材料组合的选择空间巨大,但最优设计依赖经验和复杂仿真。
制造工艺敏感: 性能高度依赖制造工艺质量(孔隙率、纤维取向、固化度),工艺缺陷易导致性能下降。
损伤检测与修复: 内部损伤不易发现,修复困难。
5.成本与性能的权衡:
高性能材料(如高端碳纤维)和先进制造工艺(如高精度模具、自动铺丝)成本高昂,如何在有限成本预算下满足性能指标是商业化的关键挑战。
大批量生产时,设计需高度考虑生产效率和良率。
6.新型布局与结构的挑战:
倾转旋翼/混合动力等复杂构型: 带来结构动力学、气动干扰、机构设计等新难题。
柔性/可变形结构: 如折叠机翼,涉及柔性机构、大变形分析、控制等挑战。
三、 设计依据点
1.设计要求和规范:
任务需求: 是设计的起点,包括飞行性能指标、有效载荷、使用环境、寿命要求、可靠性/安全性指标等。
适航规章与标准: 对于特定类型无人机,需遵循民航管理部门发布的适航标准。即使不强制适航,也应参考相关工业标准和最佳实践。
客户特定要求: 满足客户提出的特殊需求。
2.空气动力学原理:
升力、阻力、力矩的产生机制。
翼型选择、机翼平面形状设计、展弦比、梢根比、扭转角等参数设计依据。
尾翼设计(安定面、操纵面)依据稳定性与操纵性要求。
计算和仿真确定气动载荷分布。
3.结构力学原理:
材料力学: 应力/应变分析、强度理论(屈服、断裂)、屈曲稳定性分析。
结构动力学: 模态分析(固有频率、振型)、振动响应分析、疲劳寿命分析(S-N曲线、Miner法则)、冲击分析。
有限元分析: 进行静强度、刚度、屈曲、模态、频响、随机振动、疲劳、冲击等仿真的核心工具。
4.材料科学与工程:
材料性能数据(密度、弹性模量、强度极限、疲劳强度、断裂韧性、热膨胀系数、环境耐受性等)是选材和设计的直接依据。
材料加工工艺特性(可制造性)决定设计细节。
5.制造工艺约束:
所选工艺的能力、精度、最小特征尺寸、拔模角要求、装配公差链等直接约束结构设计。
6.成本与供应链:
目标成本决定了材料、工艺和设计复杂度的上限。
关键材料和零部件的可获得性、采购周期和成本是重要考虑因素。
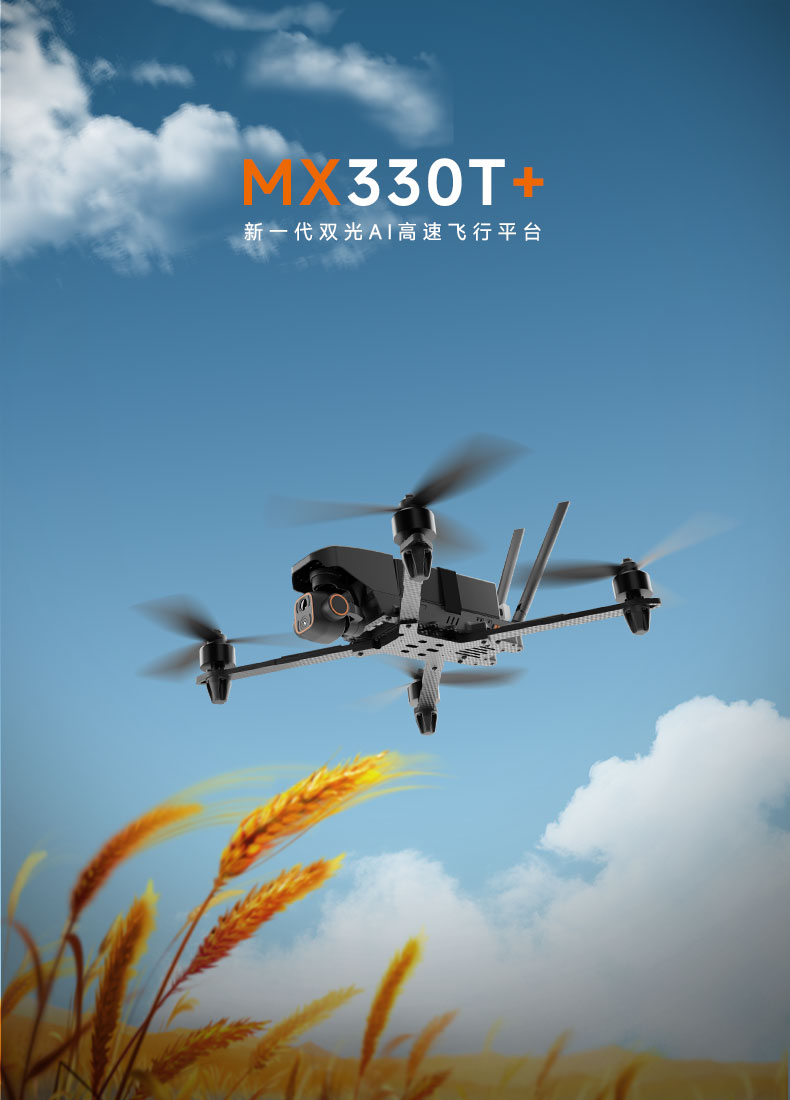