一、仿真目标
通过对优化前和优化后的布局图进行对比分析,并根据布局图进行FlexSim仿真,通过对比分析得出两个方案的仿真指标数据。从而可以确保优化后的方案理论和实际操作中都能够达到预期效果,因此可以得出如下四点仿真目标:
- 操作员的状态
通过仿真得出优化前后操作员的工作时间状态占比,作为优化前后的对比指标。
- 总的出库量
优化前后的总出库量是检验系统的运作效率的指标,总出库量越多,即代表系统的运作效率高。
- 操作员运行距离
通过仿真优化前后的布局图,可以得出各个操作员的总运行距离,运行距离越短说明操作员的劳动轻度月底。
- 设备利用率
通过仿真可以导出各个设备的利用率,通过利用率高低可以分析优化前后布局图的合理性。
二、初始仿真建模构建与运行
2.1. 建模前的基本假设
为了保证模型数据的稳定可靠,在一定程度上简化内部运行过程。以下为具体的内容说明:
- 在模型中创建的临时实体代表该车间生产的汽车零部件的原料。
- 在整个模型运行过程中,假设产品始终保持完好状态,不会发生任何错漏货损坏,从而保证仿真结果的准确无误。
- 将模型中设备的运行过程设定为无故障状态,避免模拟因设备故障而产生偏差。
2.2. 构建初始仿真模型
(1)准备工作
打开仿真模型,添加各个实体,根据布局图构建仿真模型,并用使用A和S进行连接。明确物流流向和各个作业的作业顺序,同时给每个作业区都设置一个合适的参数。通过仿真运行分析,选择合适的分析指标,并输出仿真结果。
(2)模型构建
|-----------|----|-------------------------|
| 实体 | 数量 | 说明 |
| Source | 2 | 模拟仿真汽车零部件的到达和包材的产生 |
| Queue | 11 | 模拟货物的暂存区 |
| Processor | 6 | 模拟车间的清洗、检验、烘干、装箱和产品抽检工序 |
| Combiner | 4 | 模拟车间的包装和打包工序 |
| Sink | 1 | 模拟车间的出货区 |
| Operator | 3 | 模拟进行搬运原料等作业 |
本文采用FlexSim2023版本建立仿真模型,主操作界面如下图所示:
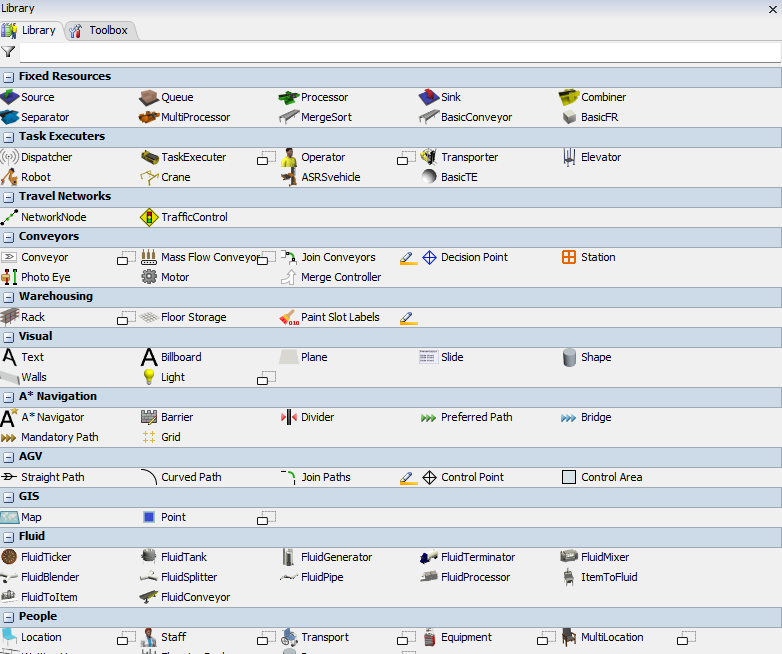
通过主操作界面上的各个实体工具,如发生器、暂存区、合成器、处理器、吸收器等实体工具对初始模型和优化后的方案模型进行仿真建模,建立优化前后的模型图如下图所示。
2.3 优化前布局图和仿真模型图
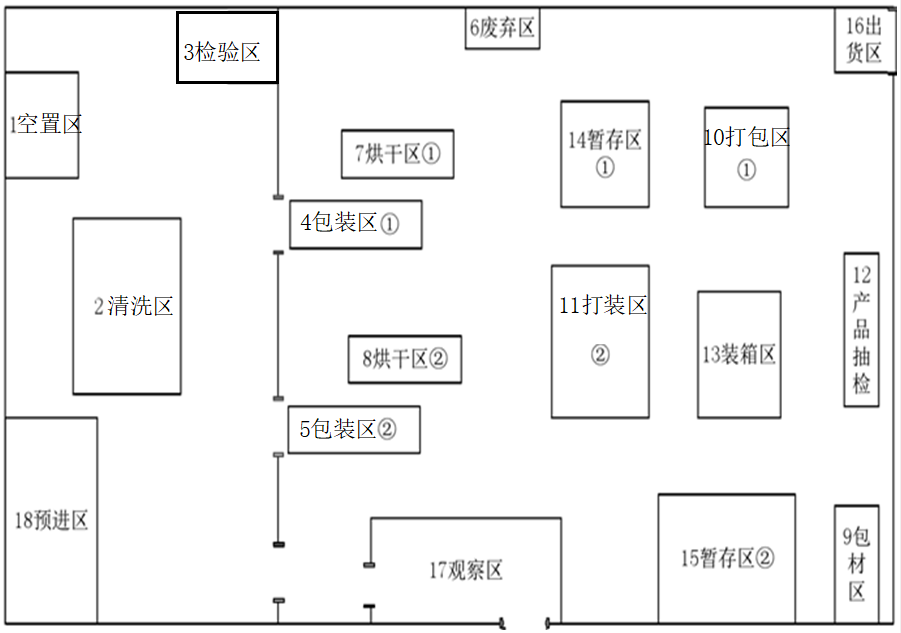
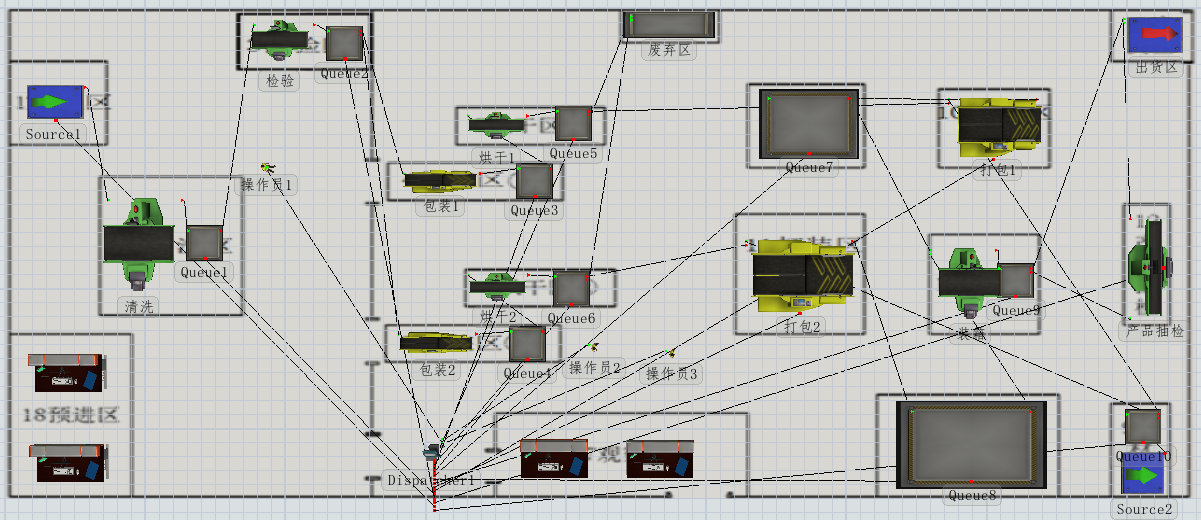
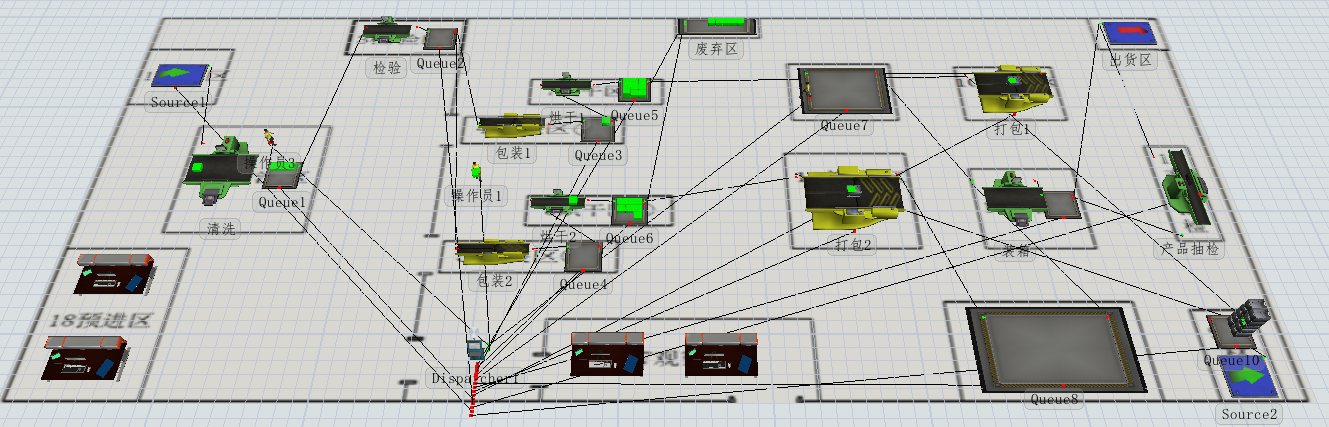
2.4 参数设置
- Source
发生器用来模拟实际原材料的到达, 是产生临时实体的工具。新增2个Source,Source1用来进行仿真汽车零部件的原料到达,设置Source1产生临时实体的间隔时间,在Inter-Arrival Time栏输入exponential(0,10),即汽车零部件的原料到达间隔时间,如下图是设置Source1的具体参数。
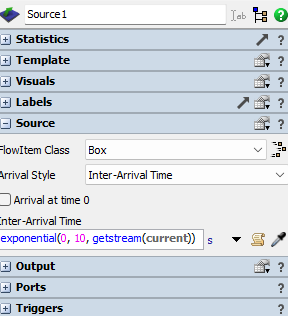
Source2是用来进行仿真提供包材的工具,假定包材无限供应,不存在缺货而影响车间的生产,因此在Source2的时间间隔设置为0,即Source2无限供料。同时在FlowItem Class栏选择Tote(周转箱)作为包材,如下为Source2的参数设置。
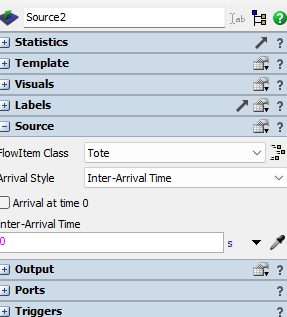
- Queue
Queue为临时存放实体的工具,新建11个Queue,作为各个区域临时存放原料的区域; 1个Queue用来模拟废弃区,用来存放不合格品,1个Queue用来模拟存放包材区域,提供打包的包材。其他的Queue分别命名为"Queue1"到"Queue10",用于各个区域的临时存放。暂存区设置最大容量500,具体参数如下图所示。

设置暂存区的搬运工具,在"Use Transport"前面打"ü",即暂存区内的原料需要操作员进行搬运动作。
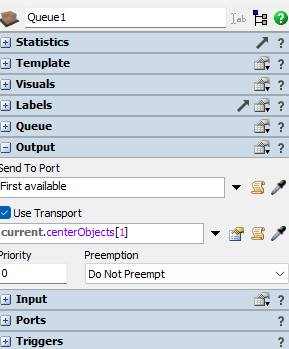
不良率的设置,原料经过检验后不良品会被发送至废弃区,因此在Queue5中,Send To Port功能栏,选择By Percentage,设置98%为良品,2%为不良品发送到废弃区,具体的参数设置如下图所示。
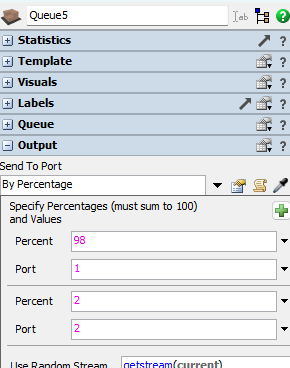
- Processor
Processor是用来进行仿真车间内的清洗、检验、烘干、装箱、产品抽检工序。新建6个Processor,Processor1代表清洗作业,Processor2代表检验作业,Processor3、Processor4代表烘干作业,Processor5代表装箱作业,Processor6代表产品抽检作业。每个处理器的参数如下表所示。
|------------|-------|-------------------|
| Processor | 模型中名称 | 加工时间 |
| Processor1 | 清洗 | Normal(32,2) |
| Processor2 | 检验 | Uniform(32,35) |
| Processor3 | 烘干1 | 68 |
| Processor4 | 烘干2 | 68 |
| Processor5 | 装箱 | Exponential(0,34) |
| Processor6 | 产品抽检 | Exponential(0,84) |
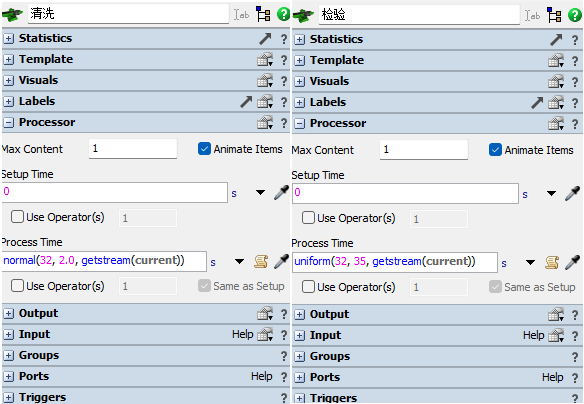
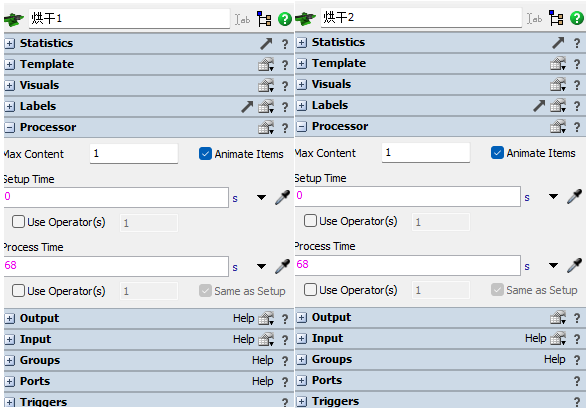
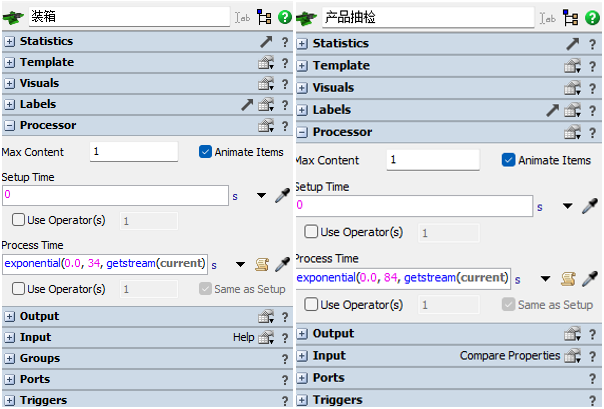
- Combiner
合成器是用来仿真打包作业,新建4个Combiner,其中2个Combiner用来进行仿真包装作业;另外2个Combiner用来仿真打包作业。点击"Combiner"在Process Time栏输包装和打包作业的时间,具体的参数如下图所示。
|-----------|--------|-------------------|
| Combiner | 模型中的名称 | 加工时间 |
| Combiner1 | 包装1 | Normal(64,2) |
| Combiner2 | 包装2 | Normal(64,2) |
| Combiner3 | 打包1 | Exponential(0,68) |
| Combiner4 | 打包2 | Exponential(0,68) |
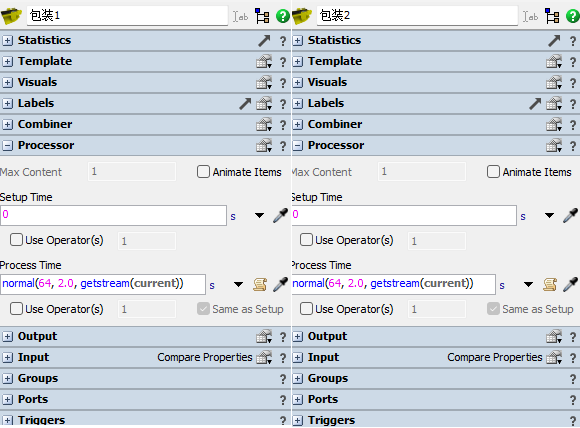
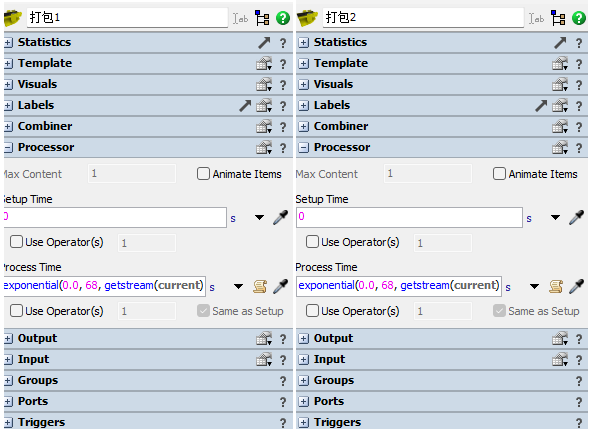
- Sink
Sink是用来仿真吸收临时实体的工具,新建1个Sink,命名为出货区,用来进行仿真汽车零部件加工完成后的发货区域。
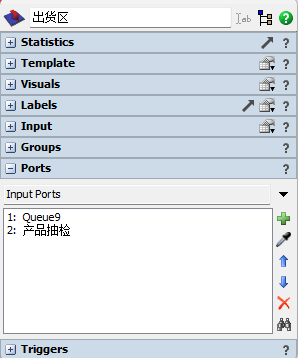
- 操作员
新建3个Operator用来进行各个区域内的物料运输,设置操作员的最大移动速度为2m/s,一次搬运1个货物,其参数设置如下图所示。
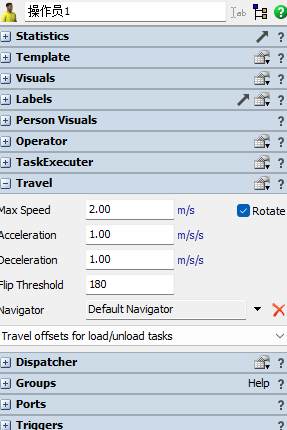
3. 优化前仿真结果
通过上述参数的设置,点击"Run Time",运行仿真,得到仿真结果如下:
(1)各个操作员的利用率分析
由如下对比饼图可以看出,优化前的各个操作员的利用率分别为93.24%、95.19%、94.20%,闲置率分别为6.76%、4.81%、5.80%。三个操作员的平均利用率为94.21%,平均闲置率为5.79%。由此说明优化前三个操作员的利用率非常高,劳动负荷以及劳动强度非常大,几乎没有休息的时间。
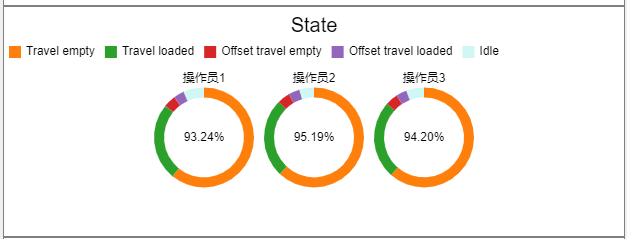
|------|--------|-------|
| 操作员 | 利用率 | 闲置率 |
| 操作员1 | 93.24% | 6.76% |
| 操作员2 | 95.19% | 4.81% |
| 操作员3 | 94.20% | 5.80% |
| 平均 | 94.21% | 5.79% |
(2)总出货量分析
通过下图仿真结果可以看出,优化前总的出库量为2969,出货量比较低。
(3)操作员的运输距离分析
通过下表可以看出,优化前操作员的搬运距离分别为484.01km、493.74km和488.99km。三个操作员的总搬运距离为1466.74km,平均搬运距离为488.91km。三个操作员的劳动强度高,搬运距离长。
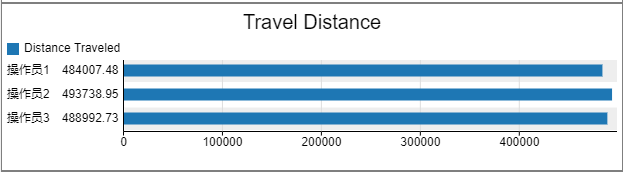
|--------|----------|
| 操作员 | 搬运距离(km) |
| 操作员1 | 484.01 |
| 操作员2 | 493.74 |
| 操作员3 | 488.99 |
| 总搬运距离 | 1466.74 |
| 平均搬运距离 | 488.91 |
(4)各个工序设备利用率分析
通过仿真结果得出如下的结果数据可看出,初始布局下,所有设备的平均利用率为39.06%,平均闲置率为60.94%。设备的利用率比较低,没有得到合理的利用,有很大的优化提升空间。
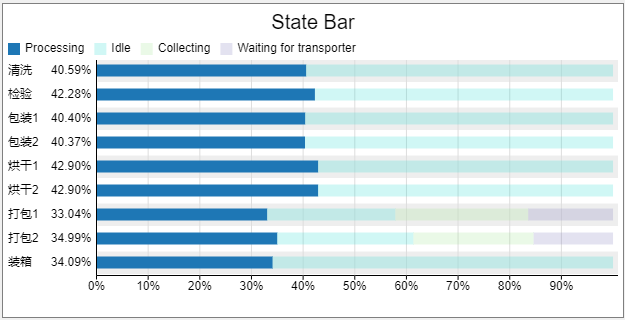
|-----------|--------|--------|
| Processor | 利用率 | 闲置率 |
| 清洗 | 40.59% | 59.41% |
| 检验 | 42.28% | 57.72% |
| 包装1 | 40.40% | 59.60% |
| 包装2 | 40.37% | 59.63% |
| 烘干1 | 42.90% | 57.10% |
| 烘干2 | 42.90% | 57.10% |
| 打包1 | 33.04% | 66.96% |
| 打包2 | 34.99% | 65.01% |
| 装箱 | 34.09% | 65.91% |
| 平均 | 39.06% | 60.94% |
三、优化模型
3.1. 初始模型仿真结果总结
-
三个操作员的利用率非常高,几乎没有休息时间,另外三个操作员的搬运距离非常长,劳动负荷很高;
-
车间的各个设备的平均利用率比较低,大部分时间处于闲置状态,有提升的空间;
-
出货区的出货量比较少,不足。
-
因此考虑以上几点,进行初始布局的优化。
3.2. 优化后布局图和仿真模型图
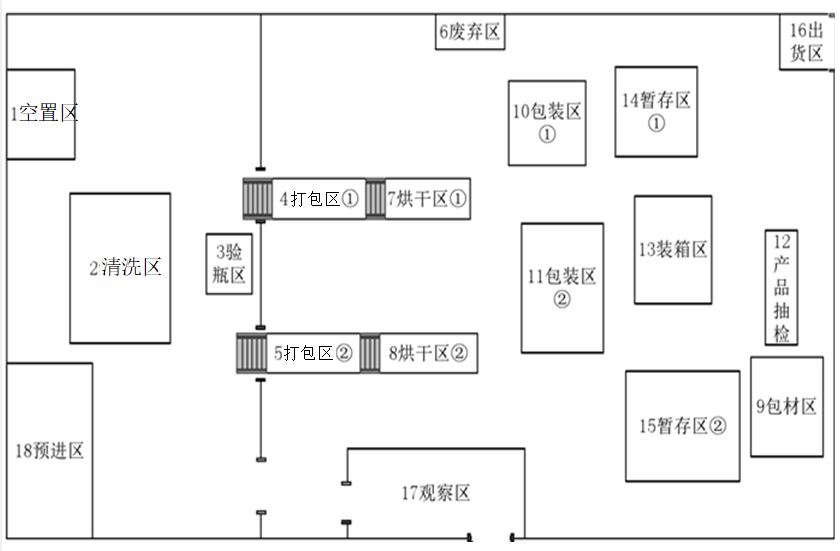
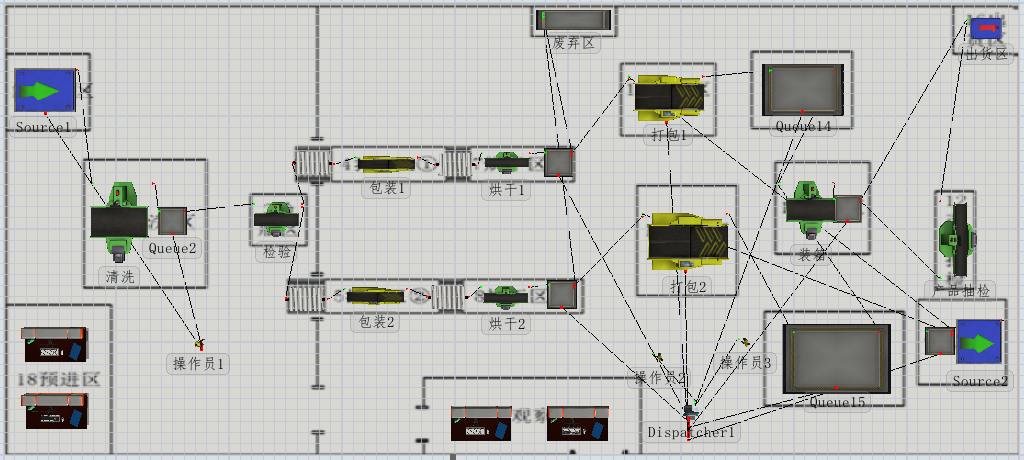
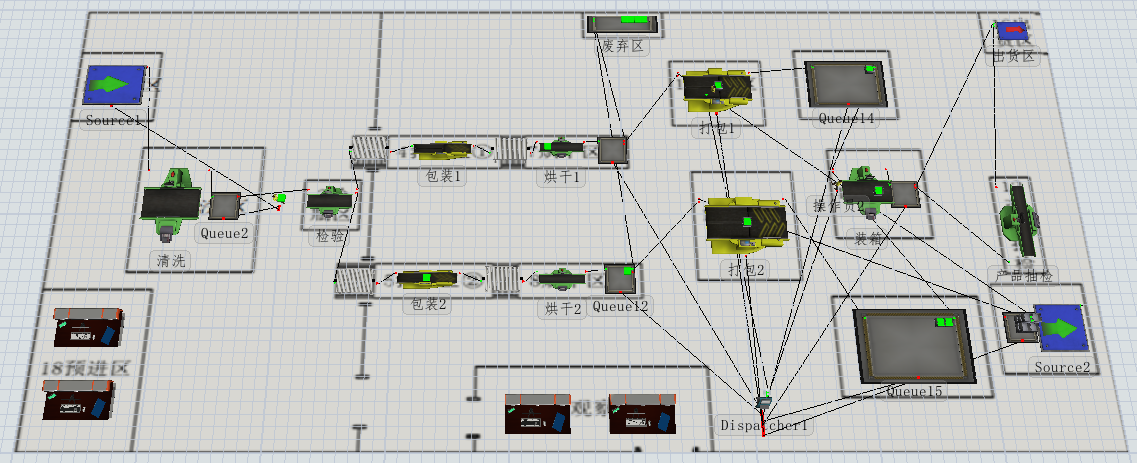
3.3 优化后仿真结果
通过上述参数的设置,点击"Run Time",运行仿真,得到仿真结果如下:
(1)各个操作员的利用率分析
由如下对比饼图可以看出,优化后的各个操作员的利用率分别为48.58%、62.47%、53.45%,闲置率分别为51.42%、37.53%、46.55%。三个操作员的平均利用率为54.83%,平均闲置率为45.17%。由此说明优化后三个操作员的利用率得到了大幅度的降低,劳动负荷以及劳动强度大幅度的减少。
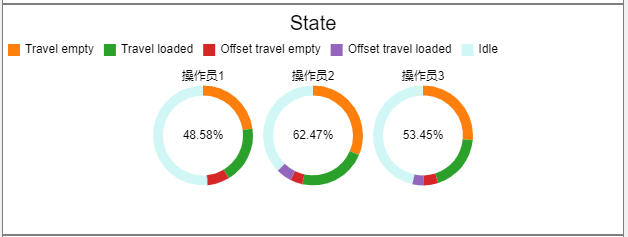
|------|--------|--------|
| 操作员 | 利用率 | 闲置率 |
| 操作员1 | 48.58% | 51.42% |
| 操作员2 | 62.47% | 37.53% |
| 操作员3 | 53.45% | 46.55% |
| 平均 | 54.83% | 45.17% |
(2)总出货量分析
通过下图仿真结果可以看出,优化后总的出库量为4302,出货量大幅度增加。
(3)操作员的运输距离分析
通过下表可以看出,优化后操作员的搬运距离分别为232.39km、306.37km和257.48km。三个操作员的总搬运距离为796.24km,平均搬运距离为265.41km。三个操作员的搬运距离大幅度减少。
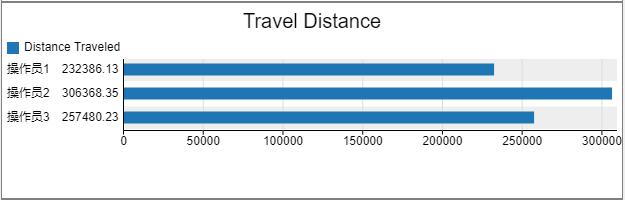
|--------|----------|
| 操作员 | 搬运距离(km) |
| 操作员1 | 232.39 |
| 操作员2 | 306.37 |
| 操作员3 | 257.48 |
| 总搬运距离 | 796.24 |
| 平均搬运距离 | 265.41 |
(4)各个工序设备利用率分析
通过仿真结果得出如下的结果数据可看出,优化布局下,所有设备的平均利用率为55.48%,平均闲置率为44.52%。设备的利用率得到了提高,
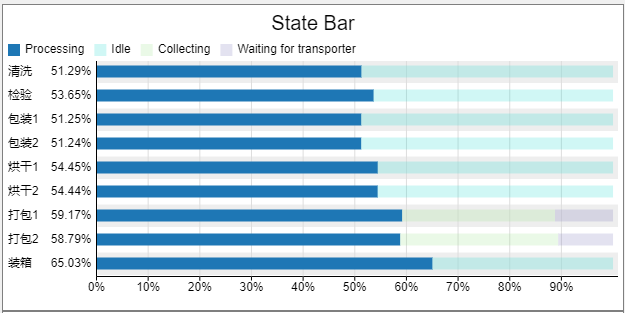
|-----------|--------|--------|
| Processor | 利用率 | 闲置率 |
| 清洗 | 51.29% | 48.71% |
| 检验 | 53.65% | 46.35% |
| 包装1 | 51.25% | 48.75% |
| 包装2 | 51.24% | 48.76% |
| 烘干1 | 54.45% | 45.55% |
| 烘干2 | 54.44% | 45.56% |
| 打包1 | 59.17% | 40.83% |
| 打包2 | 58.79% | 41.21% |
| 装箱 | 65.03% | 34.97% |
| 平均 | 55.48% | 44.52% |
四、模型优化前后对比
通过以上优化前后的仿真结果,汇总如下的表格数据,通过对比数据可以看出如下几点:
-
优化前操作员的平均利用率为94.21%,而优化后操作员的利用率为54.83%,利用率得到了大幅度的降低,操作员的劳动强度大幅度减少。
-
优化前的总出货量为2969,优化后总出货量为4302,出货量增加了1333,说明优化后的布局图,物流更顺畅,效率更高。
-
优化前操作员的总搬运距离为1466.74km,平均搬运距离为488.91km。而优化后操作员的总搬运距离为796.24km,比优化前减少670.5km,平均搬运距离为265.41km,减少223.5km,由此说明优化后的布局图路径更优,大幅度降低了操作员的行走距离,降低了操作员的疲劳度。
-
设备平均利用率由优化前的39.06%提升至优化后的55.48%,提升16.42%,说明更好方案同时提供了车间内设备的利用率。
-
综合以上几点,说明优化后的方案更优。
|-------------|---------|--------|----------|
| | 优化前 | 优化后 | 优化前后数据差异 |
| 操作员平均利用率% | 94.21% | 54.83% | -39.38% |
| 总出货量 | 2969 | 4302 | 1333 |
| 操作员搬运总距离km | 1466.74 | 796.24 | -670.5 |
| 操作员搬运平均距离km | 488.91 | 265.41 | -223.5 |
| 设备平均利用率% | 39.06% | 55.48% | 16.42% |